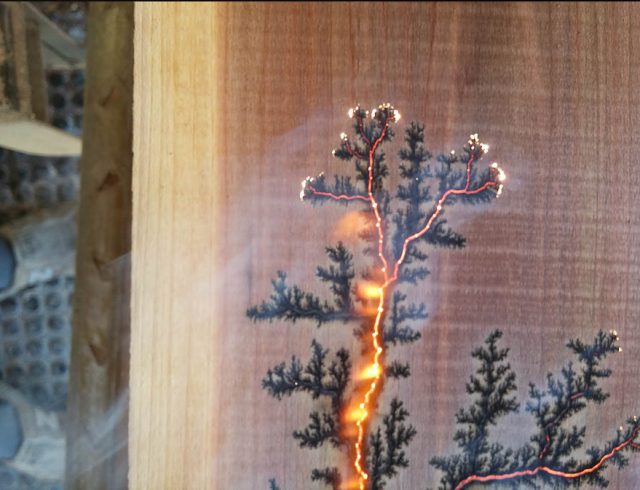
“What guy doesn’t like to play with fire and electricity?” So says Evan Blomquist, who has been doing just that for the past couple of years, as he uses fractal burning to create designs on wood.
Inspired originally by a picture of someone else doing the same thing, Evan, said, “I thought, ‘Wow, that’s awesome! I want to try that.’”
To be clear, Evan notes, “It’s extremely dangerous. I play around with about 2,000 volts of electricity. I have shocked myself once, and I was lucky to be wearing rubber-soled shoes, because that’s what stopped the voltage from making contact with the ground. So I learned my lesson, and I take all the safety precautions, like a rubber mat. I have rubber shoes, rubber gloves, al that. I cannot stress enough how careful people have to be. It’s not worth it just to burn something cool into a piece of wood if you’re not going to be safe about it.”
The machine used for this type of woodburning is made from a high-voltage power transformer. “You can find them in microwaves or oil burners or even neon signs,” Evan said. “There’s different voltages associated with whatever power source you want to choose. I just use a microwave transformer — I have a couple of them hooked together for extra voltage.”
To begin a burn, he soaks the entirety of each piece of wood he’ll be working with in a sodium bicarbonate solution. “It’s just a water-like solution that makes the wood conductive. I mean, water and electricity: two things you’re not supposed to mix, but that’s how it’s able to burn into the wood,” Evan said.
Two electrodes, a positive and a negative, are involved in the process. Evan says he places the negative electrode down on the wood for a burn, while holding the second electrode – “It has PVC pipes and rubber clamps around it and I have the [rubber] gloves on, so it’s safe.”
This is to give him some control of the design created through the burning process, which Evan describes as resembling, in general, tree-like patterns or branches of lightning. “When I touch down on the wood, it sends out, for example, five branches, and I can let that burn in for about 5 to 10 inches, and then I can pick up the electrode and move it to which branch I want it to follow. If I want it to go to the right, to the left, or straight forward, I can move it to which branch I want to continue. Then from there, it’ll spawn more branches, and then I can keep following which branch I want. Then I can make a design based on that.”
He works with wood pieces longer than a foot, “which gives the burn some time to kind of spread out and make a cool design, whereas if it’s a really small piece of wood, there’s not much design because it doesn’t have time to spread out.”
Another reason for working with the longer pieces of wood is to avoid arcing of the electricity. “If I get too close to the other electrode, I’d say within six inches, the electricity will arc between the two electrodes. It’ll arc over the wood – it won’t even burn into the wood – so it’s just like a physical stream of electricity between the two electrodes. If I had a string hanging down, or if my hair got caught in it, that would be big trouble.”
Different woods react to the process differently. Some of the favorite woods of Evan and his dad, who works with him in the business, include walnut and cherry.
Poplar, hard maple, ash and red oak, on the other hand, do not work well for the process. “If it’s a wood that has a really thick grain, the burn tends to follow the grain rather than having more of a random tree-like pattern, and it looks like straight lines. It just looks messy,” Evan said.
Other woods they’ve experimented with include honey locust, silver maple and padauk. “There’s so many different types of wood out there. Really the biggest experimentation that we do is the different types of wood,” Evan said.
It’s his dad, a former construction worker turned nurse, who brought the original woodworking know-how into the business. At the time he started this, Evan hadn’t done any woodworking at all. His dad still builds the big projects, like coatracks, bookshelves and larger tables, but Evan’s proud of his advances in his own woodworking skills.
In particular, he’s proud of a shadow box coffee table with LED lights around the underside of the lid. “That was a project that I wanted to do to kind of prove to myself that I had come a long way with woodworking. All I had when I started that project was the piece of glass. I built the lid, routed the thickness of the glass into the side of each of the rim pieces that I had burned previously, set the glass inside of those pieces, and then I built the coffee table around that,” he said.
Evan has also experimented with adding various inlays to the burns, including a glow-in-the-dark resin inlay. His inspiration, he said, came from the lightning-shaped patterns of the burns. “You know, lightning is vibrant white, or yellow, even, and so I thought it would be a good idea to try glowing in the dark. It turned out really cool, so that part of it just kind of took off – a lot of people liked it.”
He has also added inlays of malachite or turquoise stone.
There’s also a particular consideration for this type of project when it comes to applying finish. “When I burn those channels in, there’s buildup of, like, ash, carbon buildup – it’s black soot, essentially,” Evan said. “I have to make sure that I really clean that out and that there’s none left over, because if there’s little pieces while I’m staining, then it’s like a crayon taken to the wood. It can blacken up the wood and discolor it pretty severely.” He uses a wire brush to clean the soot out from the burned channels before applying a finish – his preference is for Arm-R-Seal.
After attending a large craft fair last October and receiving many custom orders, Evan said he and his dad have spent much of the winter making things from wall panels to custom coffee tables to live-edge coatracks. For Evan, the money from the Electrostatic Creations business is “my fun money to do with what I want” – other needs are funded by his nursing job. He’s a registered nurse who’s currently going to school for a higher degree.
“I think I’ll always be a nurse. I love it too much to stop,” Evan said. The woodburning business, then, is “almost like a hobby business. I don’t want to commercialize it. I really like taking the custom orders, and I really like doing the craft fairs.”
He also still likes the burning process. “Every time I burn, it’s different. No two pieces are the same. It still has that really cool factor, and I love showing people videos of the process.”
See more videos of Evan’s process on his Instagram.