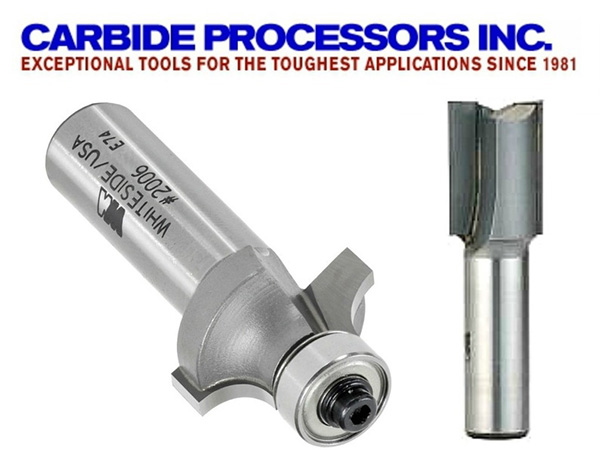
Miracle products, revolutionary tools, dramatically improved gadgets that will make your life so different you’ll hardly recognize yourself. These are the exaggerations we run into every day in the field of woodworking. All the hype makes it difficult to recognize a truly new product when we see one.
I think, however, I see one here. It’s a ceramic tipped saw blade and it’s being developed by Carbide Processors Inc., a brazing company in Tacoma, Washington, together with some of its partners. If these new saws deliver on their promises, the woodworking community could be seeing the beginning of the end of the dominance of carbide blades, router bits, and whatever else you use to cut wood.
We know this sounds like more hype. That’s why we got Tom Walz, CEO of Carbide Processors, on the phone to talk about the product he’s developing. Tom, not given to hyperbole, says about these new saw tips, “the really interesting thing about it is that they actually work.” He goes on to explain that a Japanese patent for ceramic blades was filed in 1985, but the process was flawed and the tips didn’t stay on the blade. His company has made some improvements on the process, and can now braze a ceramic–technically a titanium carbonitride–onto saw blades and keep the tips on the saws.
Better, Faster, Cooler?
So what’s so cool about ceramic-tipped (his company calls them “cermets”) saw blades? Tom doesn’t want to make too many promises, but so far the company’s preliminary tests indicate that the ceramic blades:
1. give better quality cuts
2. are quieter
3. can be sharpened to a finer edge than carbide
4. stay sharper longer than carbide
5. provide a much smoother feed
6. are especially good when you need to feed a lot of material through the saw quickly.
The quick feed capabilities can really be a time and money saver, says Tom, in professional woodshops. Tom also had Steven Kwan, a Ph.D. in material sciences at the University of Pennsylvania and amateur woodworker, try out one of these ceramic blades. Quan ran a bunch of cherry through the blade and found that it ran a lot cooler than carbide blades; that resulted in less gumming on the saw.
Early in the Game
The saw blades are, of course, more expensive, admits Tom. He compares the state of the ceramic technology to the time when tungsten carbide was just arriving on the woodworking scene. Right after World War II, carbide saw blades cost between $100 and $200, which was prohibitively expensive. Nevertheless, they continued selling and eventually became economical enough for the average woodworker. Tom says, “carbide has been around about 55 years. Cermets as tools have been around about two years.”
So, if a sea change is going to occur in woodworking tools, we’re still early in the process. And there are, admittedly, some drawbacks to cermet tipped blades. For example, they work very well cutting particle board, but don’t cut as well as carbide blades when it comes to fiberboard. Tom says, “to be real honest, we don’t know why.” Toughness is another issue. It stands to reason a ceramic-tipped blade would chip more easily than carbide. Tom says they do chip, but his company has made progress in reducing the chipping. Currently, they are as chip-resilient as some of the carbide blades, but not all of them, according to Tom.
Portland Wood Technology Show
In early tests of this technology, Tom says that even the chipped blades cut pretty cleanly. They used one on some particle board and inadvertently cut through some steel screws. The blade chipped, but still provided an acceptable cut even after the mishap. They had one of the used blades at the Wood Technology Show in Portland, Oregon, this spring explains Tom. The blade had been used in a sawmill for five months and had some chips in it where the operator had dropped it a couple of times. An attendee heard this, looked at the blade and said, “That’s impossible,” and stomped off.
Tom says there is precedent for the advent of ceramic blades in the field of woodworking. Just like in the early days of carbide blades, ceramic cutting tools have become prevalent in the metalworking trades. In machine shops and tool and die operations, ceramic tools are considered well tested and generally superior to carbide for many tasks. Now, perhaps, it’s time to once again look to the metalworking industry for superior cutting surfaces. Tom is very confident about the future. His company is so confident, it’s currently working on ceramic tips for drill bits (with router bits and shaper blades to follow).