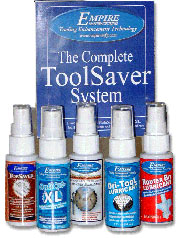
As president and CEO of Empire Manufacturing, Tim Goldberg is proud that his company’s products — with names like TopSaver, BladeSaver and ToolSaver — are helping to keep tools running clean and well in both basement shops and high-powered factories.
He has a couple of examples ready. An industrial client, a company which cuts guitar backs from 100-year-old hard Brazilian rosewood, let him try Opti-Cut-XL a spray designed, in part, to prevent pitch buildup on their band saw. Normally, the saw pitched up after 30 minutes of run time. With the application of Opti-Cut XL, it ran for a day and a half.
Pitch was also the issue in the example he cites relating to BladeSaver, which cleans and removes pitch buildup. Tim sprayed the product onto a pitched-up, burned-up saw blade, “ran my finger in circles on it, and had it completely clean in under 15 seconds.” Compared to the three to five minutes it would have taken him to clean off the pitch a decade ago, he said, “that really got my attention.”
Where Tim himself was a little over a decade ago was working as an engineer for Sandaro Industries, where products such as Top Cote, Dri Cote and Bearing Lubricant were originally developed. These machine lubricants used “Teflon suspension” technology, in which Teflon powder was inserted into different carriers and modified to meet various industry needs.
Those products made a difference: back then, companies like Western Pneumatics were only able to run 60 to 80 lugs (pieces of wood) per minute through the cutterheads on their finger jointer. A decade later, with the use of the lubricants, the rate was 160 per minute. “I compare it to cars: We took a car that was running at 25 miles per hour, and just it let go 75 miles per hour,” Tim said.
Things didn’t work out so well for him in the business world, though. French oil company TOTAL bought Sandaro in 1993, and brought Tim’s division under the auspices of its subsidiary Bostik. It wasn’t a good fit. Bostik concentrated on its automotive clients, and Tim’s wood processing industry clients weren’t the priority, they weren’t the priority. After logging 200,000 air miles, 40,000 vehicle miles and a 52-mile one-way commute to the office, Tim found that he had “turned into a person I was not at all proud of,” and he walked away.
Those wood processing industry clients tracked him down, and called him back into working to improve the running of their machines. “I’ve really done something important in the industry, and that makes my heart beat a little faster and makes me feel good about what I’m doing,” Tim said.
A couple of years ago, he also started looking at the possibilities of making the company’s products more available to the hobbyist woodworker, as opposed to the industrial companies. Woodworkers, he said, would have the same problems with their tools as industry: any cutting tool that generates heat would need cleaned, lubricated and protected. After all, he thought, a finger jointer is the same thing as a jointer/shaper — just on a larger scale.
Part of the effort to focus on consumers relates to packaging: Although it’s a cost to Empire, Tim said that putting in-use photos on the packages of the products to really show what they do “really helps consumers understand without us having to go out and teach every guy.”
Kits are marketed to woodworkers, too. A BladeSaver kit, which sells for $19.99, contains 16 ounces of the product, a cup to dip bits into, a cap for the cup, a trigger spray, abrasive pads, towels, gloves and brush. Both BladeSaver and TopSaver — a rust remover, lubricant, surface sealant and conditioner for tabletops — also come in smaller “starter packs” which retail for $9.99.
The spray option included with Empire Products is to make it easier to apply the products to bearing and cutting edges during use — or in such instances as a router table — without requiring the woodworker to touch cutting edges. Their solvents, such as TopSaver, are also non-aerosol, which means “it doesn’t deplete the ozone, it doesn’t have carcinogens, and it’s not subject to the air travel restrictions” imposed on aerosol spray shipments, Tim said.
The environmental friendliness of Empire’s products mean that their industrial clients even include the nation’s toilet paper manufacturers, who buy Empire lubricants for their paper processing because they’re waterbased and don’t have the negative contamination effects of petroleum-based products, Tim said. “Our Ph.D. chemist spent the first 25 years of his career working for the oil industry. He says he spent the first part of his career polluting the environment, and now it’s time to help clean it up.”
It’s also easy to apply things like TopSaver: spray it, scrub it, wipe it, let it dry and buff with a paper towel, is how Tim describes the process. TopSaver can clean up things like rust on tabletops caused by the oil from fingertips, and also act as a benefit in the case of friction sliding. “It goes beyond table saws, jointers, what I call stationary machinery,” Tim said. “You can use it on your hand planes.”
Empire’s latest product, unveiled this past August at the International Woodworking Fair in Atlanta, is the Complete ToolSaver kit. Advertised as an “all-in-one tool maintenance kit,” it includes TopSaver, BladeSaver, OptiCut-XL, Dri-Tool Lubricant and Router Bit Lubricant. “It gives the consumer everything needed to take care of all the needs on their equipment,” Tim said. “You can clean tools and save their life, because a clean tool will cut true, and can last a lifetime.”