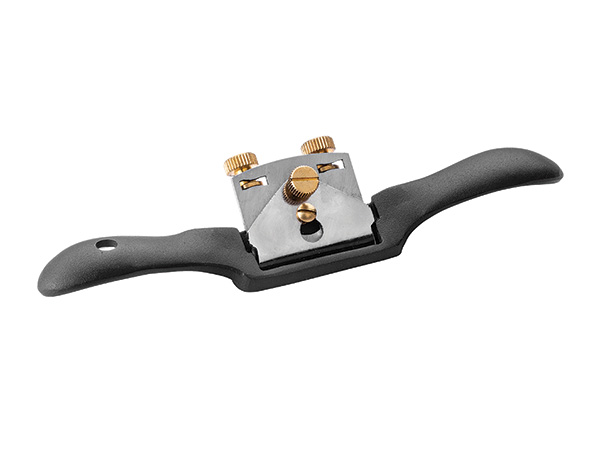
A drawknife as a roughing tool with a spokeshave as a finishing tool are yoked partners that, like a team of oxen, can get an incredible amount of work done. If setting up power tools for a job feels pokey, you might find that this hand tool duo is often just as fast with minimal setup required. These tools were used by a variety of trades for creating round stock (wheel spokes, chair spindles, pegs for post-and-beam building), stripping bark from logs (black ash for basket splint and hickory for seat caning strips), trimming the edges of leather strips and creating curved and radiused edges, to name a few.
Drawknives
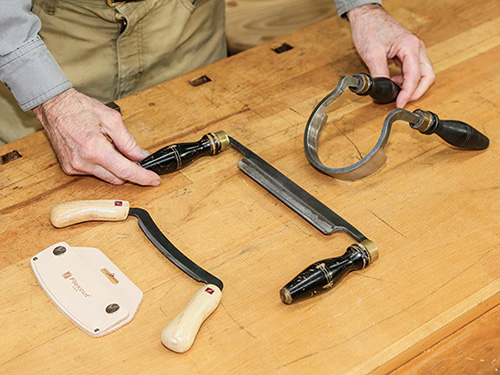
Drawknives consist of a 5″- to 14″-long knife blade with a tang at each end that is bent at slightly less than a right angle to the blade. Handles are attached to both ends. It is almost always pulled (hence the name) with the bevel up, but it can be pushed if needed. Most have a straight blade, but some are arched either upward (mostly for peeling the outer bark off of logs or coopering staves) or downward for hollowing chair seats, shovels and such. The latter, when approaching a segment of a circle, is commonly referred to amongst chairmakers as a scorp. The edge is usually a convex arc.
The drawknife is perfect for bringing a length of wood to a round or oval shape. They were and still are used in the initial phases of hewing the spindles in the backs of Windsor chairs to their unique shape. Wheelmakers and coopers also employed drawknives extensively — the former for wheel spokes and the latter to make the staves a uniform arc on the inside and outside of a barrel.
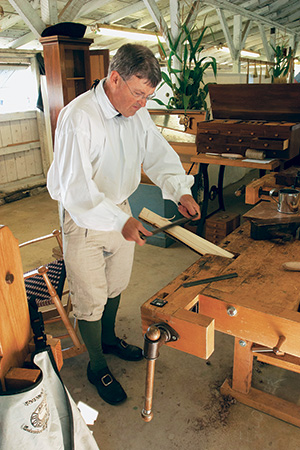
In use, the handles allow you to put your upper body and arm strength into slicing thick shavings. One must pay close attention to grain direction, or splitting the workpiece along the grain will result. Avoiding this often entails shaping half the piece in one direction and then reversing the cuts for the other half.
A number of companies still make drawknives today, and serviceable examples in good condition are some of the easiest tools to find on the antique market.
Spokeshaves
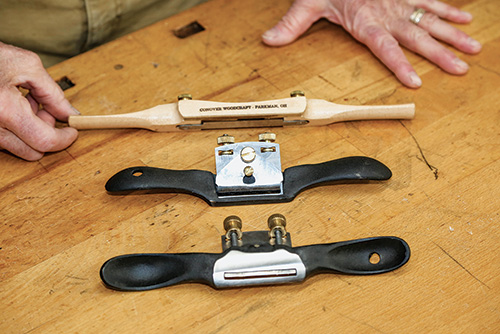
A spokeshave is a finishing tool. It refines a drawknife’s work to its final shape with a smooth surface. Spokeshaves come in two types — those with wood bodies and those made entirely from metal. The former can be thought of as a wooden jig with handles at each side that surrounds a blade and limits the thickness of the shaving it generates. Wood spokeshaves have a very low attack angle and require close attention to grain direction. Metal spokeshaves are like a small plane with the handles at the sides. The blade is secured bevel-down and bedded at about 50 to 55 degrees, making it less likely to run with the grain.
While spokeshaves are more commonly pulled, they may be pushed when necessary. Each type of shave has strong partisans.
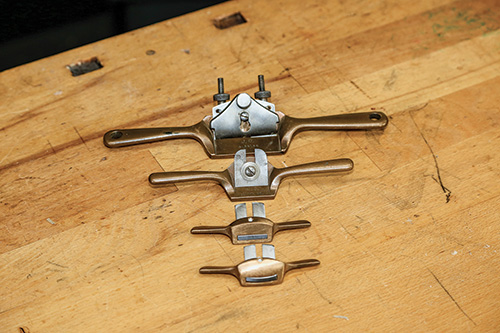
Traditionally, wood spokeshave blades had a square, tapered tang extending upward at each end of the blade. This mated to like holes in the wood stock and got tighter as it was pushed (and often hammered lightly) into place. Since the 19th century, some wood spokeshaves have sported threaded tangs that were secured with a binding post nut. A screw next to the through hole in the shave adjusted where the blade came home, thereby affecting the thickness of the cut.
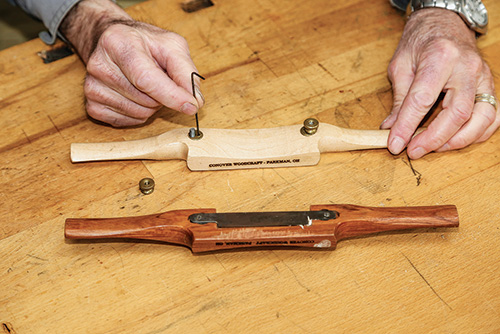
Most experienced users of wood or metal spokeshaves adjust the blade to take a heavier cut on one end (usually the left) for quick material removal. Sliding the shave steadily sideways as the work proceeds generates progressively finer shavings and a smooth finish.
Modern workers may not need to use a drawknife but may still find a spokeshave useful for an odd rounding job or to refine a roundover made by a router. Making a bullnose on the edge of a board with a roundover bit that is a bit under- or oversized for the thickness of the board comes to mind. Today, a metal spokeshave is the best bet for most woodworkers, unless they are working with green wood.