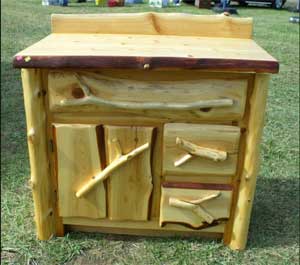
Doug Degriselles used to work as a builder for a company that built log homes. When he branched off on his own in the early 1990s, “I started filling ‘em instead of building ‘em,” he said.
Doug and his wife Mary now run Cedar-Stuff.com, where “we do it all,” he said. “We both do pretty much everything , although I do the heavy stuff, and she does most of the finish work.”
Their specialty is rustic furniture, natural products with natural edges. Partly, that is because “I enjoyed log homes. I’ve enjoyed the outdoors all my life,” Doug said. It’s also partly as a result of an accident. “I wasn’t wearing safety goggles like I should be, and a nail ricocheted off” and stuck in his eye, he explained. “When I lost an eye, I couldn’t do refined, so rustic fit right in with me.”
That choice of style also influences his wood sources. Doug and Mary will occasionally get redwood shipped in from California, but most of their wood is local, primarily walnut and cedar. “We use a lot of byproducts of other mills: what they can’t use for fine, we’ll reclaim a lot of those slabs,” Doug said. He’ll also “reclaim” wood originally destined for the fire pit – “Sometimes it doesn’t make it there, and becomes a piece of furniture” – or pick up logs from the forest floor. Doug kiln dries all his own material.
“I like woods that have defects,” Doug said. “Slabs that a lot of people won’t use because they’ll crack out, I’ll fill with stone. I like doing that because it’s different from what everybody else is doing.”
In coffee tables or dining tables, for instance, “We’ll fill a void with two-part epoxy and put stones right into it.” Doug particularly likes using turquoise for stone inlays, “because you use it with walnut, and the blue –greens really pop with the dark walnut. It’s a real nice contrast.”
In general, Doug said, “Walnut’s got a lot of natural character to it. It’s got a dark color and, depending on when you cut it, the sapwood is really light. You get the contrast between the light and the dark.” Since cedar is a lighter-colored wood than walnut, he also enjoys using the two together for the contrast.
Plus, “If you cut the tree the right time of year, you can maintain the bark edge sometimes. That’s we try to do most of our cutting in the winter,” Doug said. Right now, he’s working on an order for a customer which will use the outer round edge of logs, with the bark still on them, as legs for a bookcase. “The whole bookcase will be out of one tree,” he said.
His other customer orders have included a five-tier plant stand, requested by an Alabama bride who wanted to use it to display 400 cupcakes at her wedding. Post-wedding, “she ended up renting it out a couple of times” to other brides, before putting it to use as a plant stand, Doug said.
Although Doug and Mary have a full workshop – “planers, band saw, table saw, that sort of stuff,” he says – he flattens his slabs with block planes and, “with a natural edge, it’s all done by hand.”
The finish, Minwax® oil-based polyurethane, is also hand-rubbed. “The customer likes it because the product lays into the wood and not on the wood,” Doug said.
That approach, like the rustic furniture style, for Doug and Mary, “just fits right in,” according to Doug.