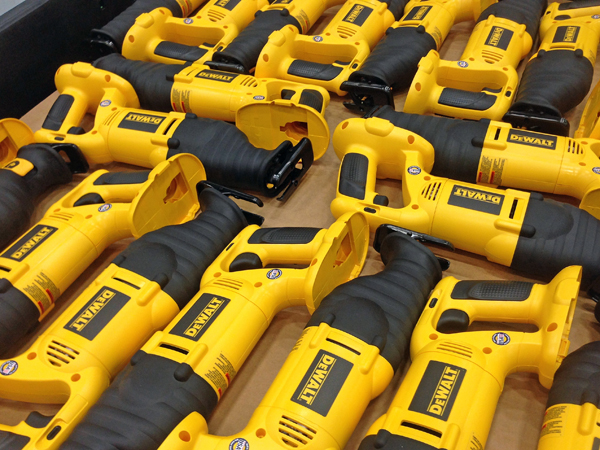
In tool manufacturing, as with so many aspects of modern life, change is one of the only constants. When markets and demands change, so must the companies that make the tools. Part and parcel with that reality, DeWALT continues a bold commitment to bring more of its tool production back to the United States again. It’s an effort to help reverse the glut of Pacific Rim sourcing for tool manufacturing that’s been occurring for decades across most of the power tool industry. It also marks DeWALT as more progressive than many of its competitors these days, in terms of shifting manufacturing back to American shores.
Identified as “Built in the USA with Global Materials,” some of DeWALT’s highest volume cordless power tools now bear labels that prove the extent of their stateside pedigree.
The latest of DeWALT’s initiatives to carry out this “Built in the USA” pledge is a 1.2-million square foot facility that straddles the North/South Carolina border. Located literally in both Charlotte, North Carolina, and Fort Mill, South Carolina, the plant has been a distribution center for DeWALT for a long time. But starting in September 2013, DeWALT cleared about 75,000 square feet of floor space and began setting up assembly cells and systems for winding electric motors. Just six weeks later, cordless power tools were rolling off the line and into carry cases and cardboard wraps, ready for consumers. It became DeWALT’s fully functional Charlotte Manufacturing Operation.
Craig Zielinski, director of manufacturing at Charlotte, says the reasoning for opening the new operation was quite simple and twofold: DeWALT has determined that it now can make cordless power tools affordably and well here in America, just as nimbly as the tools could be made elsewhere. Secondly, end users here in the States want American-made tools.
“We’re choosing to invest in domestic manufacturing because it’s important that we maintain our connection with core DeWALT customers,” Zielinski says. “Not only can we build high quality, cost-competitive products in the United States, but we also care deeply about making things at home and bringing jobs back to the United States.”
To that end, and in under two years, the Charlotte facility has created more than 350 new jobs. Equally or even more impressive still, those employees have assembled 4 million cordless tools, built 2 million electric motors to power some of them, and driven some 45 million screws to test the tools’ ruggedness.
The Charlotte facility receives around 300 pallets of supplies each day, and they quickly are transformed into assembled power tools. The fact that Charlotte is both a distribution center as well as a manufacturing plant offers distinct production streamlining, Zielinski points out. “ We can take full advantage of our flexible manufacturing cells to better respond to our customer demand. The product is available to ship to customers within minutes of coming out of the assembly cells.”
Local supplies sourcing also helps DeWALT offset higher labor costs for its American-made tools. Its “Built in the United States” branded tools are not priced incrementally higher than DeWALT tools made in other parts of the world.
Among the tools produced at Charlotte are variations of 18-volt tools and 20V Max* hammer drills, drill/drivers, impact drivers and reciprocating saws — many of which are the brand’s highest volume cordless brushed and premium brushless tools.
Some critics will take issue with the aspect of “global sourcing” for certain components that go into these U.S.-assembled tools. For instance, DeWALT’s batteries and chargers are still made in Asia and Mexico. Zielinski says as yet, “there are some components and expertise that are just not available in the United States,” despite DeWALT’s efforts to push its supply base back to the U.S. market.
“It’s also important to note that many components critical to the high quality of our products do come from our own U.S. facilities and have for many years.”
To elaborate further, readers may not be aware that DeWALT currently maintains seven manufacturing facilities in six states: Connecticut, Maryland, Kentucky, North and South Carolina and Tennessee. Those plants produce more than 600 DeWALT products, which include 48 corded and cordless power tools, 32 hand tools and 562 types of accessories (blades, bits, hole saws, etc.), according to information provided on DeWALT’s website.
“Components for DeWALT power tools have long come from Jackson, Tennessee, and Hampstead, Maryland, while many accessories are made in our Shelbyville, Kentucky, plant,” Zielinski adds.
Since opening the Charlotte assembly plant, which DeWALT coined as “Project Eagle,” the company has expanded its cordless tool efforts further with Project Eagle II. It’s focused on DeWALT’s Greenfield, Indiana, manufacturing plant, where some cordless tools are now also being made. That has created around 150 more jobs there.
All told, DeWALT employs approximately 1,800 people stateside to manufacture and distribute its tools.
Zielinski is proud of DeWALT’s production efficiencies, but equally important to process, he feels, is its people. He’s worked for numerous DeWALT plants in the past and has great respect for the work ethic and dedication of company employees. “These are hardworking people, just like the customers that use our tools on a daily basis.”
While DeWALT has not yet determined whether it will open more manufacturing facilities like Charlotte in the future, Zielinski is certain of the commitment his yellow-and-black organization has to its red, white and blue heritage.
“Today, American workers want more and more of the tools they use to make a living manufactured here in the USA. We will continue to do our best to provide them with the products they desire.”
Learn more about DeWALT’s “Built in the USA” efforts by clicking here.