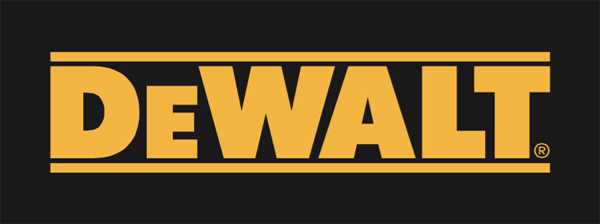
Next time you’re in the market for a high-performance blade for your table saw, miter saw or radial arm saw, give one of DeWalt’s new premium woodworking blades a spin. You’ll be impressed. I sure was, after trying them out head-to-head against other leading blades last April, right at the factory.
John Schiech and Ian Carter, presidents of DeWalt’s North American and European divisions, kindly invited me and a small group of other woodworking editors and writers to the company’s woodworking saw blade factory in Maltby, England. Maltby is located not far from Sheffield, a city synonymous with high quality steel production. It just seems right that saw blades should come from this area. Lots of tool steel for old chisels and hand plane irons did. Turns out, the Maltby blade bodies are made of UK steel, and DeWalt’s proprietary blends of C4 carbide for the blade tips come from other European sources.
DeWalt calls Maltby a high complexity, low volume plant. All facets of production are kept under one roof, so new styles of blades can literally go from design to manufacturing in a matter of hours. The manufacturing process is highly automated, which allows the plant to churn out about 13,000 blades per week – or about 700,000 tips in blade-making lingo – at full production levels. Lean and mean seems to be the name of the game at Maltby.
The company actually unveiled this new woodworking blade line last January. DeWalt’s goal was to produce high quality blades designed specifically for woodworking at mid-range prices. Eventually, the new woodworking blades will phase out DeWalt’s Series 40 and 60 blades, which are still on store shelves now. These two blade lines were originally targeted more for industrial markets than consumers and pro users.
To kick off the development process for these blades, DeWalt asked both professional and hobbyist blade users exactly what we demand from our blades. The answer, in order of importance, was accuracy, smooth surface finish and minimal tearout. These three goals became, and continue to be, the benchmarks for rigorous product testing and improvement. Above all else, DeWalt wants these blades to deliver exactly what we end users ask for and surpass what we expect. The folks at DeWalt know they face stiff competition from other blade makers, but they’re confident that these new Maltby blades can perform neck-and-neck with or even beat the cutting capabilities of other outstanding blades. From marketing to RandD to manufacturing, the DeWalt reps made it clear to us that they are just as serious about earning your tool dollars for blades as they are for high quality machinery.
More than two dozen different blades, in sizes ranging from 8 1/2″ to 15″, make up the new woodworking blade family Not surprisingly, the majority of the blade options come in 10″ and 12″ diameters. You’ll find blades suited for ripping, finish ripping, crosscutting, combination cutting and general purpose woodworking applications. The blades are engineered to cut the full gamut of materials we use in our projects, and packaging is clearly labeled to make it easy to find just the blade you need for the task and saw. If you’re a blade nut, you’ll appreciate knowing that these blade bodies are laser cut, fully hardened and tempered, then precision balanced to eliminate vibration. The tips are diamond-ground smooth so they plane the wood surface while cutting it.
So, how did the new blades fare when cutting wood? Well, DeWalt supplied us with their general purpose and crosscutting blades and comparable blades from two leading competitors. (I won’t name names, but they both start with “F”and) After loading each of the three blade types into a table saw and chop saw, they let us have at it on some 8/4 hard maple. We evaluated the cut edges by eye and using a few of the factory’s cool proprietary testing instruments. Hands down, the DeWalt blades made rip and crosscuts on par with the other blades. Tearout was minimal and so were the blade swirls. Crosscuts were nice and polished – even glassier on some passes than the competition. When the dust cleared in the room, I wasn’t the only guest nodding approval.
Aside from first-rate cutting, these blades are impressively priced. From what I can tell, DeWalt yellow is the color of a shiny new star in the woodworking blade business.