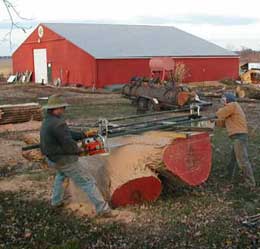
There are plenty of woodworkers creating furniture that bears little resemblance to the trees that spawned the raw material, but David Stine is different. He seems merely to coax trees into usable objects that clearly reflect their heritage. Starting from the tree itself, he crafts his pieces in a way that not only preserves the look of their origins, but preserves the forest’s future as well.
“I grew up on a dairy farm in the Midwest,” David explains, “and we did everything ourselves. That included tilling the land, butchering, building houses and even making soap. Consequently, I grew up working with tools and wood. About a quarter of our farm was woods, so there was plenty of wood for both heating and woodworking.
“Naturally, we always tried to steward the forest so that there would be ample supplies for the next generation. We are lucky that here in the Midwest, forests are very productive. With minimal effort, the forest keeps itself healthy, and there is a great variety of hardwoods. We have maple, oak, cherry, walnut, ash, sycamore, cottonwood, Osage orange and elm, among others.
“After college at Penn State University, during which I worked as a diesel mechanic, I went to law school at George Washington University in Washington, DC. I supplemented my income by making humidors during the big cigar boom. I practiced law for a year, focusing on estate work, but was still doing woodworking on the side, building tables and sideboards for people. When I would go back to the farm, I’d process lumber. Once I had enough orders, I decided to go into woodworking full-time. That was in 1996. I did woodworking in DC until 2002 before moving back to the area in which I grew up.
“When I get into a subject, I tend to delve deeply into it and learn everything I can about the field. For example, I am currently building a timber frame building for a customer of mine. He wants a furniture quality timber frame house, and I agreed to do it from local, sustainably harvested logs. I had built a timber frame with my father decades ago. At the time, I bought books on the subject and studied the field. When this job came up, I went back through magazines and books, looked online, and did more study. I don’t want to be just some guy out there hacking away.
“For me, building a piece starts with finding a tree that has died, fallen or been wind damaged. Basically, I get my wood through culling the trees. Once it is down, I skid the logs out with a tractor and get it onto my truck, which runs on a half and half mixture of diesel and vegetable oil biodiesel. Sometimes the truck smells like fried fish, and sometimes like French fries. I saw the logs with a band mill and collect the leavings for firewood, which we use to heat our house.
“I get the lumber down to the smallest thickness I can for quicker drying. Usually, the stickered wood air dries for about a year before going into a dehumidification kiln, which takes it down to about 11 percent or 12 percent. That’s what I build at. Although I have a moisture meter, I don’t get crazy about it. Instead, I use traditional joinery and account for wood movement. Essentially, I don’t try to make wood do what it doesn’t want to do.
“My design inspiration often comes during the sawing process. The slab is the star of the show; anything you do after that will only take away from it. For the Slavin bench, I hunted the woods for days just to look for the tree I wanted. I knew it was out there, but wasn’t sure where. Finally, I found an Osage orange tree right on the fence line that had almost a 90 degree bend that would fit into a corner of the customer’s terrace.
“Often I utilize big slabs for tables, headboards, and so on. I love the natural edges and often retain them. A good example of that is a line I make from honeylocust. Though they are hand planed, the tables I make from them are simple chunks of lumber. For this tree, I felt the real character of the wood was best expressed this way. All my work has imperfections in it, just like nature. Things like degrade from worm holes, in my mind, gives these pieces their interest.
“In direct contrast to that is a piece called The Wave Bench. It’s made of a series of seemingly identical shapes that, taken together, form a sculpted bench seat. In actuality, each one is hand worked and is a little different. Thus, when you walk around it, the light hits it and reveals those subtle differences and imparts a bit of movement to it.
“The inspiration for The Wave Bench came while we were having a pig roast, and all standing around picking meat off the bones. Once we got down to the skeleton, I got the inspiration from where the rib cage meets the spine. My original vision was to make it 16 feet long and serpentine, but it got adjusted down to a more manageable size to fit an upcoming show.”
Clearly, David approaches his craft as a vertically integrated activity, going all the way from the tree to the final piece. At times, it encompasses only minimal alteration, as in an oiled sycamore tree round that he offers as a coffee table. But that does not mean he does not appreciate other woodworkers and their approaches to the art. “I really enjoy the breadth of ingenuity and artistry in woodworking,” David points out. “From inlay to wood bending and beyond, people do all sorts of amazing things with wood, and I respect that.”
Along with that respect, David also shows rather a fondness for others who share his craft. “I’m often amazed at how much woodworkers of every stripe are willing to help one another out,” David mused. “Woodworkers tend to be a very generous lot.”
I couldn’t agree more, David.