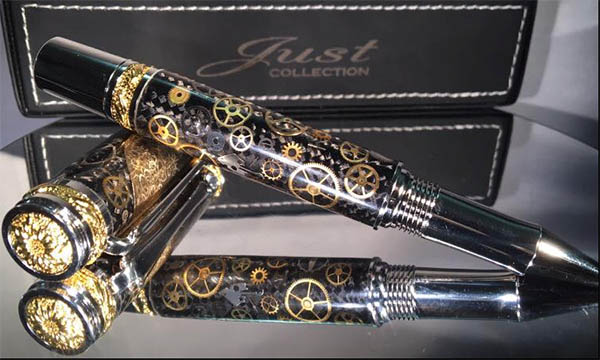
About four years ago, Danny “Will” Tricoche walked by the house of a neighbor who was turning some toy truck wheels on his lathe. “I said, ‘Hey, can I try it?’ He let me try it, and the next day, I went out and bought a lathe, and it’s been history ever since.”
Danny had not done any type of woodworking prior to this lathe inspiration – he’s now working with a JET 1221 variable speed mini lathe — saying he loved the idea but had never had anyone show him how to use the tools. After his neighbor let him try the lathe for about five or 10 minutes, “I fell in love. It was just one of those things. Danny searched out YouTube videos, brought his first project – a small turned goblet — over to show his neighbor, who told him, ‘You need to go full speed ahead,’ and has been turning ever since.
Last year, his focus turned to pens. He had brain surgery, followed a month later by back surgery, and needed to find something to do to occupy himself, but was concerned about turning larger pieces of wood. “So I got into pens, because it was smaller, it didn’t have to be a lot of weight or anything. I can sit at my chair and I can turn all day. It’s awesome.”
At first, he bought pen blanks, but quickly decided he wanted to make his own. With each project, Danny says, he tries to raise the bar. “It’s like, every time I get into a different pen, you get to learn something different. OK, so how do you do this? And how do you do that? It’s all through trial and error. That’s the best part. If you try it and it doesn’t work, you know what you did wrong, and you try it again.”
Some of his learning experiences came early on in his making of steampunk pens. “When I first started off, I wasn’t really familiar with the resin, which resins would work good with the glue. I have a few pens that, yeah, they don’t look good, but I learned from them. If you don’t let them de-gas, when you put it in your pressure pot with your resin, you’re going to have moisture, you’re going to have air bubbles. Because all those gases need to escape, and if you don’t let them, they escape into the resin and cause bubbles and deformities.”
These days, he has come up with a better process for making his steampunk pens, which incorporate things like old antique watches and watch parts that Danny buys on eBay. “When it comes to steampunk, it’s all about gears and trying to make it look as mechanical as possible, so that’s what I try to focus on. If I could make steam come out of it, I would love to do that. But that’s, you know, on my to-do list.”
Each of the Swiss movements, gears, wheels and other watch pieces needs to be bent in order to go around the brass tube that is the starting point for Danny’s pens. Some pieces he bends with his fingers; for others, which can be too thick for bending by hand, he uses a jeweler’s dapping block tool in conjunction with a one-ton press. He uses three or four different kinds of tweezers, along with small hammers, in order to place the pieces on the brass tubes for gluing. Plastic tweezers are necessary for magnetic parts. Danny will sand off watch dials, using a Dremel rotary tool to redesign them, or add carvings of his own to make the pieces unique. “I try to make everything to where nothing can be copied. I want my work to be that, if you see my pen, you know I did it.”
The brass tube is where it all starts. From there, Danny wraps the tube in materials like carbon fiber or stainless steel. If it’s carbon fiber, he waits until that hardens up to use cyanoacrylate glue and “glue each and every little piece on there until I think it’s perfect.
“After that, I let it de-gas for about a day, just to get all the fumes and everything off, and then I put it in my pressure pot, and then I use polyester resin. I pour resin over my blanks in my mold under 55 psi of pressure. I usually leave it overnight for about 10 hours. I take it out, then I let it sit for maybe about another 15 hours just to get a full cure process, and after that, I’ll put it on the lathe. I’ll turn it, sand it almost always up to 12,000-grit, micro mesh wet sand it, of course, and then I’ll polish it, with One-Step or another plastic polish, and then I’ll assemble my pens.”
‘”My main thing was that I wanted a pen that, as soon as somebody picked it up and put it in their hands, they’re going to hold it up in front of their face and they’re going to twist it and turn that pen around because they just want to see everything about that pen.” So far, that’s happened every time someone has picked up one of his steampunk pens.
Danny has also done other styles of pens, including some that have incorporated some of his own handpainted artwork: a whale, a fish and a man on a motorcycle. He also wrapped a photo of his wife around a tube and made a pen out of it. He’s also working on making a pen using diamonds, sapphires and rubies, which requires teaching himself how to set stones so he can create designs and color flow with the settings. Already, some of his pens incorporate cubic zirconia stones. Others might use materials such as Alumilite, shark vertebrae or more.
“I always try to make it different,” Danny said, “I don’t want to be the average Joe; I want people to say, ‘That’s a Danny Will pen right there.’” Known on Facebook as Danny Will, he explains, “The reason why I added ‘Will’ is because I had to psych myself up to that attitude. ‘I will do it. I will get it done. It will happen.’ That’s when I added the ‘Will’ to Danny, because ‘I will,’ and its worked for me ever since.”
Danny also tries to use his pens to encourage handwriting, recently gifting one to the winner of a kindergarten handwriting competition. “It seems like it’s just fading away. Everything is texting, smartphones. I want people to realize that it’s OK to write, to use a pen. It’s OK to write cursive.”
“This is just a hobby that I got into, and it’s turned into a passion,” he said. “It’s like a heartfelt thing that I do with my hands and just create new things.”