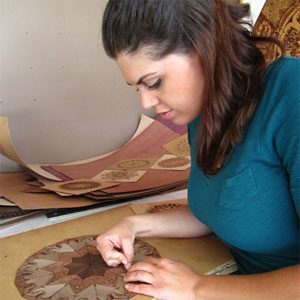
Christy Oates considers herself “an artist who works in wood,” which she describes as “a beautiful material.” Right now, much of that work is focused on the digital process, as she creates laser marquetry kits.
In graduate school, Christy said, she really wanted to get into the digital manufacturing process, in part because she was living in a very small apartment without much floor space, “so I was hanging things on the wall.” Those “things” included flat, folded furniture she created.
She created several prototypes of chairs first, then a bedside table, then lamps. In order to have the ability to laser cut her projects for her thesis show Master of Fine Arts program at San Diego State University, where she studied with Wendy Maruyama, Christy worked several hours a week for a company with a CNC router; in return, she got to cut the pieces for her show without needing to pay the $300/hour fee to rent the equipment.
That experience led to her getting her own laser-cutting machine later. Part of the appeal of laser cutting, she said, is “its exactness. It lends itself to a perfectionist like me.” That exactness also means, “there’s zero waste with the folding furniture. You cut it and put it back together as is, with a little machining around the edges.”
Her favorite piece of the folding furniture is her Crane Chair, inspired by an origami crane. “I was working with origami inspirations; everything I did, I did in paper first to figure out the folding pattern before I would mock it up in wood.” The chair shows the sort of lines and creases that you would see it you folded a paper origami crane, then unfolded it and lay it flat. Also, Christy said, when you take the chair off the wall “the crane wings aren’t spreading yet. When you get the chair to where you see the origami crane, it lets you know the folding process is completed.”
Christy considers chairs the most interesting of her folding furniture line. “It’s a nice, big piece when it hangs on the wall,” she said. “It lends itself to more of a graphic, almost like a canvas, and I can do my laser design and my marquetry on it.”
Her current focus is graphic patterns in marquetry, which she is selling as kits. “They are all repeating patterns, which could do any size,” Christy said. They came in response to inquiries she received from other woodworkers and, “my hope is that people will see these and get interested in the craft and into laser,” Christy said.
“Digital woodworking and laser manufacturing is kind of new to the woodworking community,” she said. “It’s a new tool, and it’s a different mindset from the traditional woodworker. Many traditional woodworkers are a little scared to get into the world of CNC. But it’s a new tool to master, just like a new bit on your router table, or something like that.”
Christy does, indeed, use the traditional type of power tools, such as table saws and routers, in her shop — the machining for her folding furniture is done on the router table.
And she thinks it’s important for beginning and student woodworkers to learn how to use those tools before venturing into digital woodworking. “It’s hard to introduce a tool like that and have them want to use a table saw instead of a shiny new tool,” she explained.
Christy herself got into woodworking and furniture making through school. Although she’s “worked with furniture for a long time” — her mother has a furniture reupholstery shop in the basement of her house — it was after studying interior design that Christy decided she wanted to get more involved with furniture, and pursued a Bachelor of Fine Arts in furniture design from the Minneapolis College of Art and Design.
Now, she considers herself a full-time professional artist. Some of Christy’s work is in the collection of the Renwick Gallery of the Smithsonian American Art Museum, and, she says, “I do museum shows and gallery shows and things like that. And commissions.”