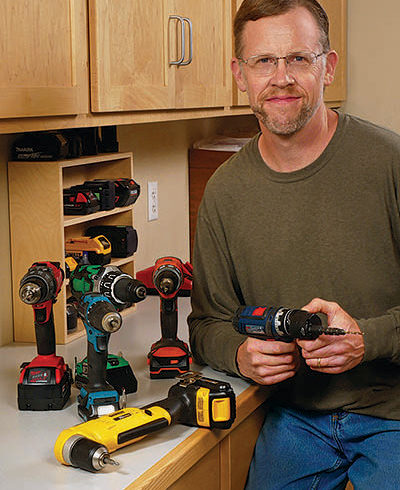
You’ve seen his name in the Woodworker’s Journal Weekly and the Woodworker’s Journal print magazine, and you’ve seen his face in various Woodworker’s Journal videos. The last time we profiled Chris Marshall in our Today’s Woodworker section was 2003. That’s … been a while.
Back in 2003, Chris was living in Ohio and working for WJ on a freelance basis. Around 2007, he joined the magazine full-time. Chris says, “My responsibilities for WJ expanded to writing new product blurbs, expert answers for the [Q&A section of] the eZine and Industry Interviews. That chance to interview what has become hundreds of companies in the woodworking products industry has confirmed to me that the people behind the product labels we buy for our woodworking needs are really passionate about woodworking, too! They want to make this craft better and keep it thriving.”
It was also around this time that Woodworker’s Journal began creating our own branded video content for our website and YouTube. “My videos were admittedly rough back then (just check out my multi-part overview of the then-redesigned Delta Unisaw if you want proof!), but transitioning from print journalism into the brave new world of social media-driven video was necessary,” Chris said. “Still, back in 2003, would I ever have imagined myself telling woodworking stories, offering teaching content and doing full project builds as a ‘sort-of’ actor some day? No way. But, it’s added a dimension to this job that, I hope, has made me a better editor and more confident woodworking teacher.”
Chris has also continued to contribute to the print magazine. “Somewhere during this latest stage of life, I surpassed the ‘100th printed article’ milestone with WJ, and I’m well on the way to 150.” Beyond the Arts and Crafts Wine Cabinet [from the August 2003 issue] he cited as a favorite project in 2003, updated favorites include a figured maple dresser “that proved ambitious in terms of the number of machine-cut dovetails it required (not to mention the wood was particularly beautiful, precious and expensive,” plus a Greene and Greene-inspired Dresser and matching bed [from the February 2016 and February 2015 issues, respectively].
Chris described those as complex projects that kept him out in the shop for many late nights and long weekends. “We all build easy-peasy projects from time to time, but those drift out of memory pretty quickly. The ones that challenge us to do our best work, or encourage us to take on new techniques that seem daunting, tend to become favorites of memory. I’m sure that’s true for most woodworkers, but it definitely is for me.”
Speaking of shops, Chris is on his second new shop subsequent to the garage in Westerville, Ohio from 2003. First, his family moved to a 10-acre property in a more rural area, the Columbus suburb of Sunbury. While there, Chris converted a dirt-floor pole barn into a heated and air-conditioned 30 x 40-ft. woodworking shop. “In the end, that space was Ground Zero for many, many tool reviews and project builds.
“I’ll never forget the time we rounded up 10 or so cabinet saws for a big tool review, and suddenly the shop became a parking lot for a group of what were then some of the finest cabinet saws on the market. What an amazing ‘problem’ to have had – a woodworker trying out a showroom’s worth of premium table saws, in the privacy and convenience of his own shop, and then sharing that feedback with our audience. I was the luckiest guy I knew.”
Then, in 2011, an opportunity in Chris’s wife’s career moved the family from Ohio to the foothills of the Blue Ridge Mountains. “The one crucial feature our home here in Virginia didn’t have when we bought it was a garage – much less a woodworking shop. So, my current 20 x 40-ft. shop was one of the first orders of business when we settled here. While the size and capability of the shop was somewhat dictated by budget, I also wanted my shop to look like the shops of our readers. Essentially, it’s a garage with many of the benefits and limitations that go along with sharing a woodworking space with cars and other stuff.”
If he had to do it over again, Chris said, he would install only one roll-up garage door instead of two, prioritizing more wall space over more vehicle access. He’d also add outlets and ceiling fixtures. “You can never have too many clamps, or outlets, or lights, and I would put all three of those items at the same level of importance,” he said.
Still, the shop does have one feature that never appears in videos or article photos: a large window on one side with a distant view of mountains. “The opportunity for me, in the middle of a big project or video shoot, to look out that window and see the serenity of a mountain view, is a continual reminder of how lucky I am to both do this work and do it in such a beautiful place. In that regard, I’m still the luckiest guy I know!”