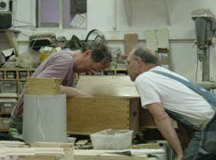
Ask most woodworkers to name the one thing they dislike about furniture making, and there is a good chance they will answer “finishing.” It seems to be the bane of woodworkers, and even those who are good at it admit they see it as the least pleasant part of the job. That’s not at all the way it is at The Workshop Of Charles Neil.
“I love finishing,” Charles admitted. “People sometimes ask me why I do woodworking and I answer, ‘so that I can finish it.’ A good finisher can make a bad woodworker look good, but even a good woodworker cannot make a bad finisher look good.”
As luck would have it, Charles is both a good finisher and an outstanding woodworker and furniture maker in a wide range of styles. While his love of finishing may set him slightly apart from many of his contemporaries, his view of how the woodworking world approaches that task takes him even farther afield.
“In my opinion,” Charles told me, “the learning cycle in woodworking is backward. You should learn finishing first. Finishing is not something you do after the piece is built, but rather part and parcel of the building process. It is too late to start finishing on a piece that is already completely built. For that reason, even though I love finishing, I won’t do it for others.
“When you design a piece,” he continued, “you must also design the finish at the same time and take that into account. If you approach it that way, you will learn to put a finish on a raised panel before you put it in the frame, and if you are going to attach a molding, you’ll learn to sand the molding and everything behind it before you attach it.”
Neil’s background and early job experience helps to explain both his affection for finishing and for his latest endeavor, selling jigs. “I grew up in a little town called Stuart’s Draft, Virginia,” Charles recounted, “back up against the mountains. I lived with my mother, an aunt and my grandmother on a farm. Until I was seven or eight, we did not have indoor plumbing. We heated with wood cut on a sawbuck with a crosscut saw. I never had store-bought bread or milk until I went to school. We went to town once a month for staples, and it was a big deal.
“We had a vocational school nearby where you could spend part of your school day taking electives. I took woodshop at the age of 13 and really enjoyed it. I discovered that I had a knack for woodworking and it came easily to me. I continued taking shop throughout school whenever I could, then went home and did more woodworking in my spare time. As luck would have it, I had inherited a set of tools from my grandfather.
“When I got into high school, I took an auto body class, and found I really liked that as well. Down the road from me was a guy who painted cars, and he taught me to spray. I found spray guns instantly comfortable, and finishing cars was my strength. After high school, I got a job as finisher in an auto body shop and worked there for the next 18 years, building furniture at home in my spare time.
“By 1989, I was living in Charleston, South Carolina, and had just finished a complete rebuild on a brand-new Mercedes. It had been in a huge accident with only 19 miles on the odometer. The owner had just pulled out of the dealer’s lot when he had a run-in with a dump truck. I finished that car with a multi-layered lacquer buffed to a fare-thee-well; a real custom show finish.
“I realized that this was the pinnacle of my automotive art, and I guess that did something to me. As soon as the car was done, I put down my tools, turned in the keys, loaded up my truck and went home. To this day I have never again done body work.
“I moved back to Virginia to a little cabin on the mountain, set up a woodworking shop, and started building things. Over the years, I’ve built in a wide range of styles: Mackintosh, Hepplewhite, Shaker, Colonial, Federal and even modern. I’ve made everything from dovetailed beehives to coffins and just about everything in between. I started taking my work out to local craft stores, and sure enough, people started buying what I’d built. Almost immediately, people started asking for custom pieces. These days, virtually all my work is commission.”
With such a wide range of pieces and styles, I wondered if he had any favorites. “My favorite thing to build is beds,” Charles told me, “in part because I have built so many that I have it down to a science, and in part because I like the beauty and simplicity of the form. I can make a canopied pencil post bed, admittedly a modern adaptation, in just a couple of days, provided I have a lot of coffee.
“Along the way, I designed and developed a slick pair of jigs for cutting the eight tapered sides to make a tapered octagon post. With these jigs, you can do four posts in just a couple of hours. One thing you learn growing up on a farm is being innovative. You don’t think about buying things, but how to do what you need to do with whatever you have. Consequently, I’ve invented a number of jigs, two of which are patented, though four more are in the patent process.”
Then came teaching. “I first started teaching about five years ago so other local woodworkers would stop interrupting me during the day asking me to show them how to do things. I set up some classes in my own shop for about half a dozen at a time, and they filled right away. Teaching was immediately satisfying. It is hard to describe watching the joy of someone who made something important to himself or herself for the first time.
“At that point, I had grown into a larger shop with five or six employees. Things got way too hectic, so I moved to a smaller shop, got rid of my employees, and took a break from teaching for about three years just so I could catch up on back orders. It is only in the past few months that I have gotten caught up.
“Because I love the one-on-one contact of teaching, I decided a few months ago to start again. Starting in September, I’ll be teaching one-week classes in making a Virginia sugar chest, which I feel is great for beginners because it has tapered legs, drawers, breadboard end, lock, keyhole, applied molding and dovetails. For the first time this year, I am also offering a finishing class, and I am amazed how many people want to sign up for it.”
Out of teaching came a newsletter, DVDs, and his latest venture, selling jigs. “I also realized early on that it is much more efficient to simply record what I do and put it on DVD,” Charles explained. “I simply run a camera out in the shop and show things. The production values are simple, but the information is top-notch. If you’re looking for a fancy studio and polished actors, keep looking. However, just as all my furniture is guaranteed for life, the DVDs are, too. If you feel you did not get your money’s worth, send it back, and we will refund your money and pay the shipping. It’s probably worth noting that we have never gotten either a DVD or a piece of furniture back.
“Though I have used jigs all my working life, selling them is brand-new to me. So far, only the Pro-Am EZ Taper Jig is being sold, and that came about mostly because of a class on tapering. Nine of the ten people in one class said they would not use the common taper jig sold by many companies because they saw it as inherently unsafe. I came up with my version, and they liked it. I used it on a DVD, and I started getting phone calls from people asking to buy one.”
Along with more jigs, we can probably expect to see a lot more teaching from Charles, judging by what he has to say on the subject. “Lately,” he admitted, “building furniture has gotten to be less of a joy and more of a labor. I realized that it is time for me to take my 40 years of woodworking and finishing and share the information with others.
“I teach basic and simple. I don’t get into theory, history or chemistry. My goal in teaching is to remove the complication from woodworking and finishing. Tell them the truth, show them right, and keep it simple. Get it done, and get it done right.”
Those are wise words from a man who clearly heeds his own counsel.