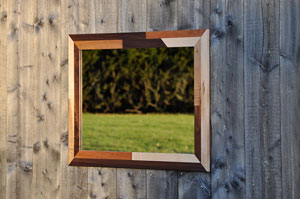
When it comes to his woodworking, Brian McAlpine says, “I try to let the pieces themselves be my voice.”
Brian didn’t set out planning to be a woodworker; instead, after gaining a degree in mechanical engineering, and then having trouble finding a job in that field, he went into metal fabrication for a while. “One of the projects involved wood at some point, and I fell in love with the wood side of it, and decided to pursue it,” he said.
Brian took a three-month workshop at the North Bennet Street School in Boston, purchased some equipment, and then set up shop in the back area of one of his previous metalworking employers. “I had never used things like joiners or planers, so I went to North Bennet Street to learn those tools, and also hand tools,” Brian said.
As he works, “I usually go back and forth between hand and machine tools,” he said. “I usually stick with pretty simple construction: mortise and tenon and some dovetail.” It’s not necessarily the mechanics of constructing a piece that has the most appeal for him: “I like to see a piece design in my head, and I want to get there.”
That might incorporate an interesting grain, or another natural element. “My favorite type of stuff is doing casework, sideboards or credenzas,” Brian said. “The shape allows a box and then a front with doors or drawers that I’m able to use as my palette.”
That might include incorporating unique boards into the design — Brian says he’s previously been doing a lot of work with live edges and natural forms — or itmight include creating a pattern. “Moving forward, I hope to do more pattern work,” he said.
His most recent piece, for example, is an ash and walnut cabinet with a Southwestern design in veneer on the front. Brian recently completed a course in veneering with Brian Reid and Thomas Hucker at the Center for Furniture Craftsmanship, and looks forward to creating more patterns on veneer in the future.
When he’s looking for ideas for the designs themselves, he said, “I reference, as much as I can, nature, and the designs of the past. The Southwestern one came from a wool rug pattern, so it’s looking at other types of designs and trying to blend that into wood.”
As for which woods, Brian says he has always tried to work with only domestic hardwoods. “Walnut is always my favorite, but it’ssometimes hard to find locally. Lately, I’ve been quite interested in ash. Traditionally, we’ve always thought of ash as not as modern, but I’m trying to use it in a more modern fashion. With the new waterborne finishes, they put a whiter finish on it, and it doesn’t yellow as much, so I’m introducing that into some pieces.”
Brian does try to use natural finishes with low VOCs, “but the most important part of ‘sustainable’ is to make sure everything I’m building is good quality furniture built to last, and not end up in a landfill in a couple of years like a lot of modern furniture.”
He also cites a coffee table that he made using two boards of rotted ash. “The legs come up through the top, so I could cut the rotted area away. It allowed meto use wood that was essentially firewood.”
Brian also has a line of pieces he calls “Leftovers,” whose purpose is to use up scraps. “It’s taking everything left over in the shop and trying to put them together in a jigsaw puzzle type pattern,” for the creation of tabletops, for instance, he said. He keeps his offcuts in a box and, “Every other month or so, I try to go through the box and put a piece together.” This might be a tabletop, small decor pieces like candleholders, or “little jewelry pieces to use up even the smallest pieces.”
Those pieces speak for Brian, and for his love of woodworking. That, he said, was inspired by “the warmth of it, rather than the coolness of metal, and just the way it worked with wood.”