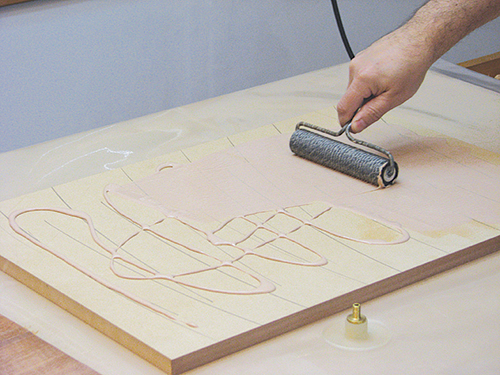
I have recently been asked to build a conference table from zebrawood veneers. I have a fully outfitted professional shop but have never used veneer. I am not interested in purchasing a vacuum setup for this job. I have ordered 20 mil, paper-backed, 4’x8′ sheets of veneer. In all the research I have done, I discovered that there seems to be a controversy regarding the ‘best’ adhesive to use. I will be using an MDF substrate and most likely a shop-made veneer press using clamps and cauls. The piece is essentially constructed of flat panels. What is the problem, if any, with using a quality contact adhesive on the paper-backed veneer? Some of the hardcore veneer craftsmen insist that using contact cement on paper backed veneers is ‘unholy’. Any advice based on personal experience would be greatly appreciated.
Ian Kirby: You can view each part of a woodworking project as a link in a chain. Apart from all else, these steps are uniform and they work in concert. And we all know how strong a chain is.
Thin veneer on paper is part of this chain ? in this case it’s an industrial chain designed to give high yield at low cost. The veneer is sliced thin to bypass sanding, which is always a costly affair. It is attached to the substrate using a specially formulated contact adhesive which is sprayed on, giving an even, uniform thinness. The veneer and substrate are joined and passed through a polished roller at high pressure. Some veneers have a microthin foil layer under the paper to prevent finish solvents from delaminating the veneer at the glue line. It’s a great system, but unless you have all the links in the chain, you’re courting failure or at least a mediocre result.
Frankly, I can’t imagine this conference table falls into the class of product put together with contact cement (which is not an adhesive since it never cures). My personal experience with contact cement is that surfaces come out lumpy because the cement is too thick and uneven. The veneer press doesn’t help a lot because the cement won’t flow ? as will an adhesive ? and it’s not permanent. The cement never sets (like the sun on the former British Empire). It’s important to remember that veneering is a chain of events that we understand and can control.
Ellis Walentine: It sounds to me like you’re heading for double trouble. First, a conference table is a big piece to veneer (although you didn’t mention the size of the largest glue-up), and you’re likely to have a tough time getting enough pressure, distributed evenly enough, with just clamps and cauls.
Here’s the arithmetic based on a 2′ wide glue-up: If you figure a pipe clamp can exert a maximum of 1,000 lbs. of pressure, the maximum pressure your beams can exert on your flakeboard cauls is 1,000 lbs. For the pressure to be distributed evenly across the cauls, you’ll have to crown your beams (plane a belly on the surfaces that are in contact with the cauls) to compensate for the expected deflection of the beams under end pressure. This is a complicated calculation in itself.
Now, assume you use enough layers of cauls to evenly distribute that pressure across a 6″ wide section of your table, for a total of 144 square inches of glue surface. Dividing 1,000 lbs. by 144 works out to only 6.9 lbs. of pressure per square inch (psi). A vacuum bag exerts one atmosphere of pressure, or 15 psi, and you don’t have all those heavy waxed cauls plus beams and clamps to deal with.
Second, regarding glue, I am one of those people ardently opposed to contact cement for veneer. You can’t be sure of getting it down tight without air bubbles, and any joints in the veneer will be susceptible to swelling and opening up with changes in relative humidity. I’ve heard horror stories of whole kitchen jobs that had to be replaced. The glue that is most preferred by most experts for veneering work is Unibond 800, a two part adhesive that gives you enough assembly time and bridges any slight gaps between veneer and substrate. Personally, I use yellow glue for relatively small veneer jobs where I can work quickly enough. I’ve also used powdered plastic resin glue because of its long open time, but I don’t advise it for very porous, blistered or wrinkled veneers. It doesn’t bridge gaps very well. Finally, your best bet for this project would be to locate a commercial cabinet shop somewhere in your vicinity that has a hot press. Most people who own these contraptions will be glad to lay up the top for you. Tape up your face and backing veneers, and truck everything over there for glue up. They use a special thermosetting PVA glue that sets in about 5 minutes, and the job is as good as it gets. They might even be willing to sell you the flakeboard for the substrate, saving you the hassle of buying and schlepping your own board around.
Rick White: There are a lot of issues here. I’ve used contact cement on veneers, but never with such a big surface. The size of this project spells trouble for many reasons. If you want to use a contact cement that’s water-based, it’s going to soak into the veneer and cause all kinds of expansion and contraction problems. And with this paper-backed veneer, you could end up only gluing the paper, not the wood, to the substrate. So I would go with a hard glue.
That said, you’re also going to need a pretty big press with a lot of clamps and cauls to get a good result. If you skimp on the clamps, you’re going to get bubbles.
If I were in your shoes, I’d take the project to a plywood manufacturer. There are a lot of them around, and one of those shops will have the equipment and know how to make you some zebrawood ply that will do the job. And a plywood manufacturer will probably be able to do it cheaper with better results than if you try to hack this out yourself.