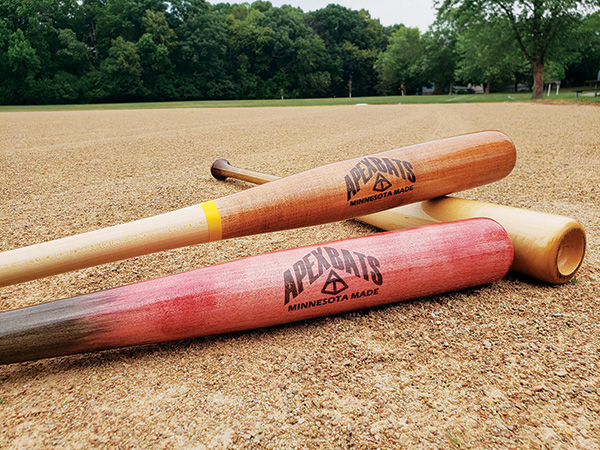
“From a woodturning standpoint, making wooden baseball bats is actually a pretty basic technique,” says Dan Little. “It goes from billet to bat on the lathe.”
His 12- and 14-year-old sons both play youth baseball, and Little keeps busy during practices by whittling in the stands. A couple of years ago, he set himself a challenge of making a “fungo bat” — a long, slender bat that coaches or parents use during practice. “It’s something I’d use with my kids, so I just thought, ‘this is something I want to try,'” Little says.
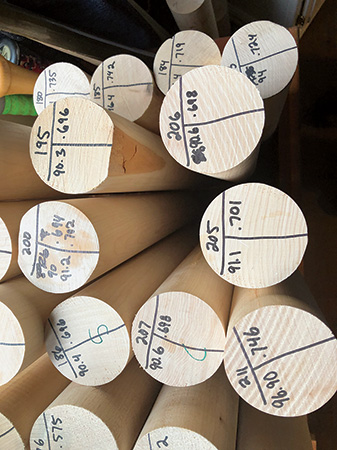
“As soon as I made that bat, the kids were like, ‘well, I want a bat,’ so they each got a bat,” Little says. Then he showed one to a coworker whose son also plays baseball, and got another request, “and then it just started to escalate from there.”
An engineer by day, Little has now made about 200 bats in his garage workshop for his apexbats.com side business. He starts with billets of maple or ash, or upon request, birch or beech. “I only make game bats with the best possible grade that I can get,” he says.
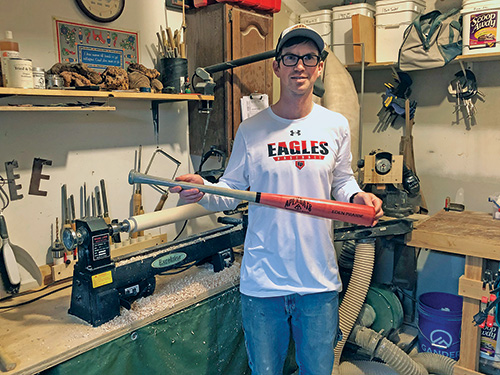
Most critical for purposes of bat-making is the density of the wood, which, in combination with the bat’s design, impacts its weight. Bats for adults generally use higher density wood — sometimes extra dense if it’s meant to be a heavier training bat — while Little tends to make kids’ bats from lighter, lower density pieces.
He also tests the quality of the wood using an ink dot test. This involves putting a drop of wet ink on a piece of bare wood, then observing how far it deviates from a center line as the ink bleeds.
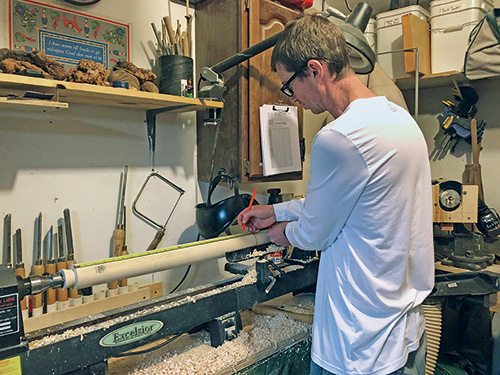
He’s adapted this test from a Major League Baseball requirement that the ink bleed no more than 2.86 degrees away from the center line. “It’s really just saying, ‘Is your grain straight in this wood?'” Little says. “If it’s not, then it’s gonna have much more likelihood of breaking. I don’t want to have a kid break a bat because I used poor-quality wood.” Because bats are made one at a time, customers can choose how the weight is distributed through the barrel of the bat (whether it’s balanced or end-loaded): the bat’s length and weight; how much the knob tapers for their personal comfort; and barrel and handle diameter. “Some like it to just feel a little thinner in the hand, and some like it to feel a little thicker,” Little says. “If there’s a model that I’m finding is a very popular combination, I’ll make a story stick that has all the key points,” he says. “It’s really quick for me to grab that, and it cuts down a lot of time.”
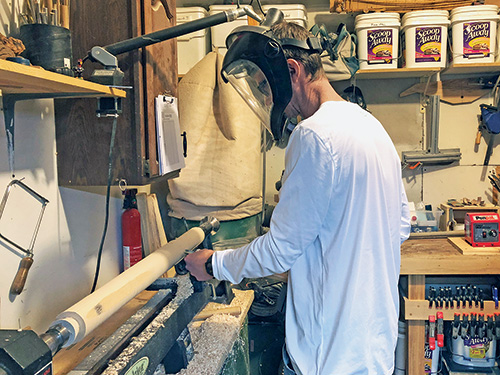
Customers can also choose to have the bats “cupped,” or somewhat hollowed out, on the end. Cupping a bat, Little says, can help remove some weight or balance a bat out so it swings a bit lighter. “I start by drilling a center hole, then I use a router with a guide pin to cut out the rest, and then I go back with a larger drill bit to drill it out again, because it leaves kind of a core.”
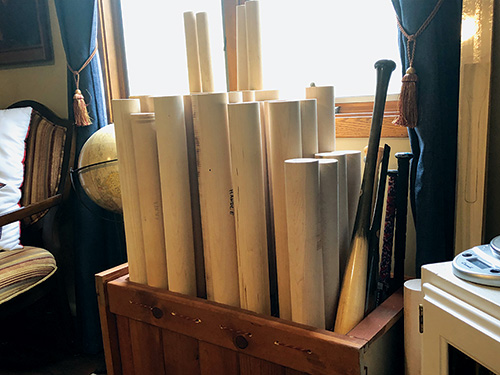
Customers also get to choose the colors of their bat, for which Little uses oil-based stains applied by hand. He’ll burn in personalized messages with a small laser engraver, and he applies the Apex Bats logo with an ink transfer using freezer paper. “I tape that to an 8×10 sheet of paper and print it off in a mirror image, then quickly flip it over and rub it on. I like the way it looks, and it’s embedded into the wood, so it’s never gonna come off,” Little says.
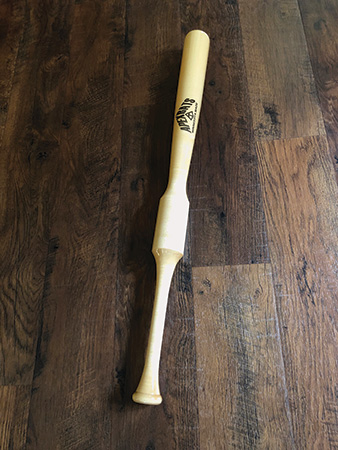
Most of the bats Little makes are game-quality bats; about half of them are for kids. While he’s not pursuing the lengthy and costly process to become an approved bat vendor for Major League Baseball, Little is reaching out to town ball teams and has made bats for wood bat tournaments. “I don’t know if it’s a nostalgia thing, or if people are just looking for something different,” he says.
A version of this article originally appeared at: eplocalnews.org.