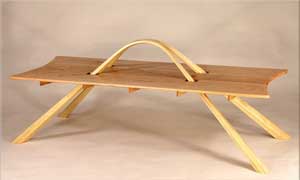
For Andy Pitts, woodworking is a second career. In his first career as a U.S. Navy officer, he was an engineer trained to operate both a nuclear reactor and surface ships. With that background, “I’m a very linear thinker,” Andy said.
In 1976, after building a bookcase for himself and his wife, Andy decided he really loved woodworking and that it was “something I’d like to do the rest of my life” — and began to plan accordingly. “From that point on, I was learning about woodworking and collecting tools.”
After retiring from the Navy in 2002 as a captain, he built his own workshop, went through the legal necessities “to call myself a business,” and started doing craft fairs and farmers’ markets, and joining organizations to get his name out there.
At first, “I started out building pieces very square: tables with right angles, and so forth. Then something happened — I’m not sure what — and I started thinking more in curves.”
For instance, a rolltop desk he built several years ago for an architect is “very rectilinear,” Andy said. His first successful piece after his migration toward curves, the “Chest Sans Sides” — in which the drawers are the sides of the chest — is “curved and graceful. I got into bent laminations and complex joinery. I rarely do straight anymore,” he said.
For the most part, however, Andy focuses on collaboration with the clients for his pieces. “What really drives me is what the client wants. I consider myself as the guy who can make it happen,” he said.
Part of his collaboration sometimes involves helping the client figure out what it is they do want — as was the case two years ago, with clients who had a large persimmon tree on their property that needed to come down. “We were able to get 14″ wide planks out of it,” Andy said. “It’s unusual for a persimmon to get that large.” The clients knew they wanted something built from the wood, but weren’t sure what.
“It turned out that what they could use was a large shelf unit to display some pottery, with some drawers, to go on a large wall space where a grand piano used to be.” By resawing poplar into 1/8-inch strips to build up a core, then veneering the persimmon to the outside, Andy was able to create a bookcase type unit with curved sides — and a height dimension of 72 inches.
Andy owns a WoodMizer LT15 sawmill and a solar kiln, which allow him to create and dry lumber from trees on clients’ property. “I like to use clients’ trees,” he said. People call him if they are building a house and a tree needs to come down, or if a tree is dying. And, despite forestry being one of the main industries in his area of Virginia, “I don’t cut down any trees just to make lumber. I don’t have to.
“I live in Virginia along the Chesapeake Bay. A lot of hurricanes and Nor’Easters come through, and constantly blow trees over. People know I have a sawmill, and they call me; if it sounds like good furniture wood, I take it.”
One client’s wood is still in the drying process, but it has an interesting story. The walnut tree came down during the building of an addition onto a house that had been in the family of Chesapeake Bay watermen for generations. As Andy was milling the wood, “I heard the pitch of the saw blade change. It wasn’t steel — I recognize the sound of a nail. I lifted the plank off, and it looked like someone had used red caulk to caulk up the tree. I’d never seen that.
“It turns out it wasn’t caulk; it was Grandpa’s boots” – the red rubber boots worn when pulling oysters. “When he finally retired, he left ’em in the crotch of the tree, which is where he left them every night to dry out. The tree grew up around them, andI was cutting through them.”
It’s likely Andy will try to incorporate that “red caulk” into whatever the final destination of the walnut turns out to be. “I always try to do a new technique and a new challenge with every piece,” he said. He has experimented with ebonizing, on pieces like a “Shadows of the Night” chest with cattails and dragonfly, and has also been putting carvings into his pieces lately.
In fact, shortly after he’d taken a class on carving at the Center for Furniture Craftsmanship from British carver Chris Pye, a church in New Jersey contacted Andy with a request for him to make a Paschal Candle Stand with carvings on four sides.
The stand needs to support a candle that’s over 30 inches tall and usually about 2 inches in diameter, used at times like Easter, Christmas and other special days in the church. The carvings on all four side panels of the Candle Stand for the New Jersey church were favorite motifs of the people for whom it was a memorial. Andy has done Paschal Candle Stands for other churches as well, including his own, and says he enjoys doing such liturgical work.
Of course, he’s also still coming up with other ideas. He’s a member of the Furniture Society, which Andy touts as a great way to network and, during the 2006 annual conference in Indianapolis, he participated in a bus trip excursion to Columbus, Indiana — a town, where, in the mid-20th century, the leaders of local business Cummins Engine led the push to make the city a showcase of architecture. One of the sights on that bus tour was the Interstate 65 Gateway Bridge, “and someone on the bus said, ‘Someone’s going to build a table that looks like that bridge.'”
Andy, in fact, built two of them: one from ash, cherry and red oak; the other from cherry, holly and red oak.
“The artistic part is what I try to put into the project,” Andy said. “I don’t try to gravitate toward any one thing.”