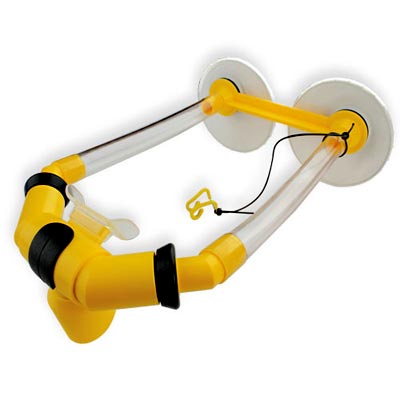
Jim Duxbury, in his life pre-retirement, worked with scuba equipment. He’s also an avid woodworker and woodturner, and one day he got fed up with the respirators he was wearing to keep the dust out of his lungs. So he drew on his knowledge and experience and came up with what he calls the Resp-O-Rator, a device that takes a radical look at current respirator designs and tries to make some dramatic improvements.
Traditionally, this column has interviewed toolmakers who have been in the business for a long time or who turned a good idea for a tool into a whole business, or who are major designers with the large tool manufacturers. Jim isn’t any of those. He’s just getting started with his Resp-O-Rator and is still wrestling with issues of production, patents and making everything work. He’s got a working prototype of the respirator, but they aren’t available yet. Nevertheless, we thought it would be interesting to find out what a new toolmaker, still in the throes of creating the product, was thinking about.
Right now, he’s thinking about all the hassles in the way of getting his design into production. “It’s beyond words how much trouble it is,” says Jim. One of his speed bumps is working with plastics and injection molding. There doesn’t seem to be any process for getting the parts exactly right, so there’s been a lot of trial and error with the company making the parts for the Resp-O-Rator. Learning how to write a patent was also a learning experience Jim doesn’t seem eager to repeat.
But once you get him talking about the respirator itself, you can see why he does it. The original problem that caused him to create this safety device was his inability to use traditional respirators under the clear plastic face shield he preferred to work with. He had to get the filters off the front of his face, so he ran them around back. He also didn’t like the weight of traditional respirators, so he took the straps off : most of the weight of his breathing system rests on the shoulders of the user. These filters counterbalance the front of the respirator so, Jim says, it’s almost weightless.
It’s also designed to be used by bearded woodworkers which, to his surprise,has made the design very popular in Amish areas, where long beards are ubiquitous. He’s demonstrated the device in Amish counties and received enthusiastic responses.
Jim’s done demonstrations at woodworking stores and shows in the Ohio area and customers are very interested in getting their hands, and mouths, on one. “When you get it out, they laugh. By the time you put it back, everybody wants one,” says Jim. The counterbalanced design allows the mouthpiece to lightly rest in the mouth, he explains, so you don’t bite down on it.
The other improvements he’s made to traditional respirators attest to Jim’s perfectionist nature. He buys better, more expensive filter material so it keeps out 95 percent of all particulates. He says it’s actually higher , but the National Institute of Health and Safety won’t let him claim that because it doesn’t have a category for it. His filters have 45 square inches of filter material, while existing respirators only have 13 square inches.
He’s also designed it with one third the dead air space inside the mask, so when you intake air, you get a lot less of the air you’ve already breathed.
This was particularly important for Jim as a woodturner because of the amount of dust he creates when he’s turning. He says he has a small shop and big lathe, and when the dust starts flying, he really appreciates being able to use both the respirator and his face shield. Since he uses a lot of spalted materials, black walnut and exotics, the Resp-O-Rator keeps him safe and healthy. Of most wood dust, he says, “none of it’s very good for you, to be honest. And they are only just finding that out.”
As Jim Duxbury enters the toolmaking business, he’s relying on his passion for his product to carry him past the obstacles he faces. With luck, he hopes to see the Resp-O-Rator in a woodworking store or catalog soon.
– Bob Filipczak