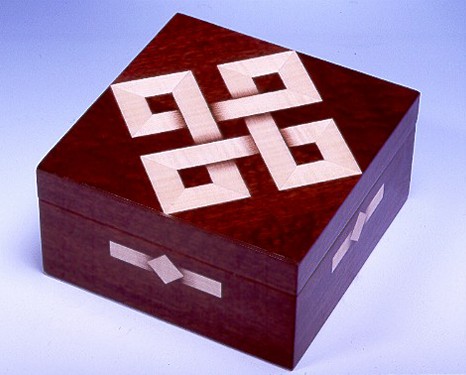
Most people will throw it all away for a shot at the big time to become an actor in New York. John Russell is just the opposite. He was an actor in New York for 30 years and decided to quit the business and follow his true love: woodworking in the form of marquetry.
John was from a show business family in Los Angeles-his father was a stage and film director-so he went into the family business as an actor. About 10 years ago, he says, “the squeak was out of the toy,” and he quit acting to try to make a go of making art with veneers.
He first picked up marquetry as hobby when he was in an antique store. He found a notebook in the shop and the cover of consisted of a map of South America, done in marquetry, with a different wood for each country. He was fascinated and wanted to learn more.
When he moved to New York, he went down to the Bronx and a visited Constantine’s, a venerable business that was famous among hobbyists and woodworkers. This was a shop that started in 1812 on the Bronx docks and was in the business of certifying woods that came in on ships. It recently went out of business in New York but one branch is still open in Florida.
Anyway, John found books on marquetry, veneers and glue. So he tried his handat the craft and liked it. That was 30 years ago and he’s learned a lot since then. “Marquetry basically, if you really cut to the chase, is painting with wood. So I have a full palate of colors and textures and grains to work with which is just extraordinary,” he says. A quick look at his webpage will reveal wood veneers you’ve probably never heard of, and John says he currently works with about 100 different veneers. He says he learns something new about wood every day.
One of the things he has learned is called sand shading. He says the French invented the process about 500 years ago when they were first experimenting with marquetry. The process involves heating beach sand in a skillet, as hot as possible, and dipping pieces of veneer in the sand, so it burns without charring. “I decided to try it out and it worked like a charm. So about half of my designs employ a little bit of shading in order to get a three dimensional effect,” says John.
In terms of a hobby, this one was ideal for him and his first vocation: acting. Marquetry doesn’t take a lot of space, doesn’t require a lot of power tools and it was something he could take on the road with him when he was touring. He used to make the boxes himself but that became a hassle, so he now buys them from his friend, Dennis Parrot, at Valley Woodworks. He doesn’t even use a vacuum press for the veneer, preferring to use contact cement. He hasn’t run into any issues with that adhesive except in the case of unstable wood like macassar ebony. The contact cement doesn’t hold it in place as well and the lacquer eventually cracks. So John has quit using that wood.
But he doesn’t avoid all obstacles. He swears by lacquer for his finish, even though he says, “it’s very difficult. It’s the devil’s liquid.” John explains that as lacquer dries, it gets thinner and more brittle. So he used to use at least 10 coats of the devil’s liquid. After watching it more carefully, he noticed that it works better if he starts with six coats, waits 10 days and then adds another seven coats. “After ten days, what you thought was an absolutely perfectly smooth lovely surface, now you can see the grain and the lines between two given pieces of woods,” he says.
The other trouble he runs into is the way lacquer works with different woods, absorbinginto different veneers at different rates. “You put a couple of coats of lacquer on a burl, like walnut burl or redwood burl, you might as well be putting it on a paper towel. It just sinks and disappears,” he says.
With that said, John admits there’s nothing like lacquer. “I decided lacquer embellished the natural qualities of the wood. It really brought out all the colors,” he says. Not bad for the devil’s liquid.
– Bob Filipczak