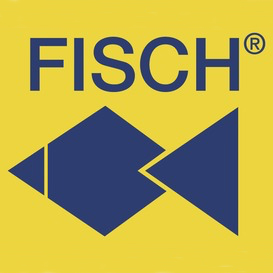
When Tony Hinch first introduced the vortex drill bit, he knew it was a good tool. But he didn’t know how good until a professional woodworker contacted and told him he had cut 30,000 holes with the bit without sharpening it and it was still cutting well.
On the one hand, says Tony, that was his goal when he took over Fisch back in 1992: to make quality tools that really stood the test of time. But he has to admit that when tools last that long, “I’ll never sell him another one.”
Tony joined Fisch after doing a bunch of consulting work designing high-tech automation lines for GM. While he was used to high-profile projects (billion dollar projects for the car manufacturer), the challenge of taking a small start up company was simply irresistible. He always had a love of woodworking and he always worked with tools of some kind, so he jumped at the chance.
Fisch (at that time spelled Fish) was a company that imported some of the highest quality tooling in the world. This tooling is made by Johan Eberhardt in Austria, and Tony really liked the idea of bringing the best tools in the world to U.S. woodworkers. For example, Fisch’s Forstner bits are guaranteed for life. That’s right, for life. His company sells about a quarter million Forstner bitsevery year and he can only remember six times when a bit was returned by a dissatisfied customer.
In the first six years, Tony grew the business by 1,500 percent. Then about two years ago, the Austrian company wanted Fisch to exclusively carry its tools and that wasn’t the direction he wanted to go. So he bought out the Austrian interest in the company and is expanding the business based on his vision. He continues to import the high quality tools from Austria and is Eberhardt’s biggest distributor.
Tony believes that woodworkers want great tools that last. So he’s currently working on building new tools, especially some new power tools, that compliment the tools he already carries. For example, he’s just introduced a new benchtop mortiser that features an extra large pinion gear so you don’t have to sprain your arm while cutting a mortise in a particularly tough chunk of wood. They recently tested on a 2.5″ piece of oak and it resulted in less than a thousandth of an inch deviation in the wall thickness from top to bottom. His company is also about to introduce a floor model mortiser as well as a large lathe.
Woodworking shows have been a good source of information for new products for his company. He goes to shows to gather input and find out if his products on the mark. “The people in woodworking aren’t bashful about what they want. And if you screw up, they’re not bashful about telling you either. But they’re also not bashful about spreading good news and we rely on that.”
Tony also runs into a lot of price pressure when he goes to shows. Woodworkers want quality but they don’t always want pay for it. For example, his mortiser costs what comparable machines cost, but his competitors throw in the mortise chisels. His mortise chisels, because of the quality, cost $160, so he can’t really afford to give them away with the mortiser. “There’s pricing pressure to reduce the overall quality of some of the machinery on the market?something’s got to give. It’s usually motor windings or strength or something or other. You can’t build the quality we used to build 30 years ago in this country and make it affordable at a price point at some of the big box stores,” says Tony.
So now, Fisch is embarking on a new set of tools called the Guildcraft line. These are designed to provide high-quality, accurate tools at an affordable price for the new woodworkers. They won’t last forever, says Tony, but they will give the novice great tools that will work the way they are supposed to. In the meantime, his company will continue to develop and built tools that will stand the test of time. “We want the machines to last. They’re not supposed to break down the day after the warrantee is over. We don’t plan for them ever to break down,” says Tony.
– Bob Filipczak