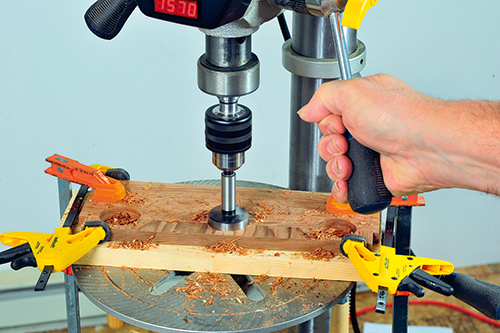
I’ve been attempting to mount a standard Jacobs chuck on the tapered spindle of my drill press. But every time I put stress on the chuck (e.g., twist a bit in a heavy material), both chuck and bit come free of the spindle. How can I overcome this problem?
Michael Dresdner: First, check that the spindle and chuck are the same taper. If they are even slightly off, the chuck won’t seat properly. Once you’ve ascertained that the fit is right, take them apart and inspect them for smoothness. If there is a ding on either the female (chuck) or male (spindle), smooth it with fine 600 sandpaper and refit. (If the mating problem is between a male chuck spindle and the female drill press quill, the same rules apply.) Finally, clean both the female and male sides of the taper. Sometimes, a bit of machine oil can get on one part or another, and that will prevent the taper from seating securely. Cleaning the male portion is easy, as you can get to it with a towel and a bit of mineral spirits. The female portion is a bit tougher, but woodworking suppliers sell a special taper cleaner that looks like a neon colored plastic twist bit. Once the two parts are clean and smooth, set the chuck on the spindle and press the parts together, either with a clamp, vise, or use the drill press itself, pressing against a scrap board on the drill table.
Rob Johnstone: I can’t be sure, but it sounds like you don’t have the correct taper for your drill press. These tapers have obscure names like a #2 Morse, but the bottom line is that the taper on the chuck must match the shape of the taper in the drill press. If they don’t match exactly … well, you get the idea.