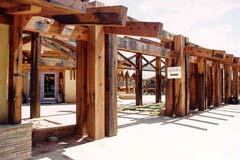
On May 10th, 1869, the tracks of the Union Pacific and the Central Pacific railroads met at Promontory Summit, northwest of Ogden, Utah. There, the famed golden spike was driven into a laurel tie in a ceremony celebrating the completion of the first transcontinental rail line going from the Atlantic to the Pacific.
By 1901, Edward Henry Harriman had acquired both railroads and set out to bypass the worst bottleneck on the line, 100 miles of tortuous track climbing the mountains around the north end of the Great Salt Lake. Starting in 1902, he built a shortcut called the Lucin Cut-Off that went directly across the huge lake. Trains began using the cut-off on March 6th, 1904, and it soon paid for itself in savings.
The crowning glory of the Cut-Off, and an amazing engineering feat for its day, was a 12-mile-long wooden trestle spanning the lake. Building the Lucin Cut-Off trestle used a veritable forest of trees: 30 million board feet of mostly Douglas fir and redwood. It did yeoman service, but as it aged, it became more and more expensive to maintain, and in the early 60s, was replaced with a solid fill causeway, essentially dividing the lake in half. To this day, the northern half of the lake is saltier, and shows up a different color on aerial maps.
All that wood was simply left standing in the lake until 1993, when one family started hauling it out to make it available to woodworkers. John and Alice Cannon, the owners of a construction company founded in 1972, were given the opportunity to salvage the wood from the Lucin Cut-Off trestle. Along with their four sons, Joe, John, Fred and Bob, they created a subdivision called Trestlewood to process and sell this remarkable wood.
“Trestlewood is unique,” explained Joe Cannon, one of the sons, “because of its high mineral content from being in the Great Salt Lake. Wood from above the water looks like standard, old growth Douglas fir, but the wood below the waterline offers far more unique color variation. The minerals in the material have penetrated to the core of the wood, leaving streaks of colors from pinks and purples, to blue, gray, and black.”
“Our initial intention was to wholesale the wood in bulk to existing wood processors,” Joe said, “but we found there were none that were able to handle the quantities we were talking about. In addition, others did not want to put salty, mineral- and metal-laden wood through their machinery, so we developed our own machinery and processes to deal with it. We focus mainly on wholesale sales to lumberyards, flooring distributors and contractors, and encourage customers to work with our retailers, but we will sell direct if no other outlet exists.”
Though lumberyards don’t stock Trestlewood, the company works with customers via a toll-free number (877-375-2779) to direct them to a local distributor. They find out exactly what a customer needs, then drop ship the wood from either Idaho or Utah.
It took the Cannons from 1993 to 2002 to get all of the wood out of the lake. Much of it has been sold, but there is still about seven million board feet left. The family, along with about 30 employees, does the primary processing on 50 acres on the lake near Promontory Point. From there, wood goes by truck to a 17-acre facility in Idaho where they make everything from flooring and timber posts to lumber in all of its forms.
The salvage effort was not without its challenges. “On the trestle, there were thousands of massive 14 inch by 14 inch timbers,” Cannon told me. “One of the problems with these pieces was that they had dozens of one inch metal pins connecting them to other timbers. We needed to remove the metal and resaw these into more useable lumber sizes. Fortunately, our subcontractor, Idaho lumberman Emil Hein, invented a hydraulic machine that latches onto the metal pins and pulls them out without further damaging the timbers.” Most of that wood went to companies building exposed timber frame houses, and all of it has now been sold.
Salvaging the trestle wood became merely the starting point for what is now an ongoing business. “After having created a structure for processing such wood, it made sense to broaden our horizons,” Joe continued. “While I was in law school in Chicago, I kept my eyes and ears open for other salvage operations.” Along the way, they have salvaged and processed Southern yellow pine decking from a Spiegel warehouse in Chicago, heart pine from a Chicago cold storage building, Douglas fir timbers from a plywood plant in British Columbia, and both Douglas fir and redwood planks from California pickle vats.
“We’ve purchased material from literally dozens of other projects from New York to Alaska. There will continue to be a demand for this sort of product because of the ecological benefits, as well as the fact that most of it is old growth and of a higher quality. Matching up a customer with a product that brings their project together and makes them happy makes it worthwhile for us.”
“The reclaimed wood business is an exciting and fun business to be in,” continued Joe, “because we are able to do unique projects that have both ecologically sensitive and historical sides to them. As long as there is wood to be salvaged, we’ll be in the business.”