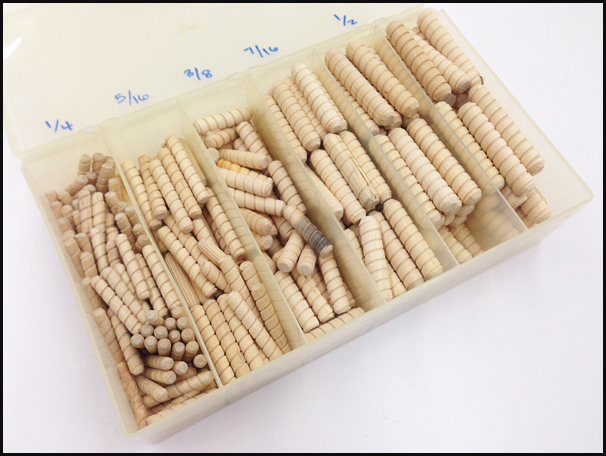
I make jewelry and utility boxes from scrap wood and often have trouble finding wide, thin pieces for the bottom and lid. I hate the waste and wear on my planer just to shave a piece of 3/4-in. stock to 1/4-in. or less. I have butt joint dowel kits but none of them go below 1/4-in. diameter dowels. So I have two questions: 1. Why don’t dowel kits go less than 1/4-in. in diameter? 2. What is a recommended method of joining thin wide pieces of wood that is aesthetically pleasing? – Mark Bauer
Tim Inman: Dowels do come in smaller diameters than 1/4-in. I have one that goes down to 1/8-in. dowels. You can make your own smaller dowels, too. Why don’t the jigs go smaller? Probably because furniture makers seldom use smaller ones. Set yourself up to use whatever size you want.
Personally, I use dowels only as a very, very last resort. They don’t offer much strength, and they really don’t hold well over time. I have been a professional furniture restorer and conservator for over 50 years. In that time, I’ve seen many, many failed dowel joints. For me, and I think for you, too, biscuits would be a much superior joining method. They do offer superior strength in the joint and at least as much help in aligning the surfaces of two glued boards. I have a Makita “mini” biscuit joiner. Its intended use is small joints and picture frame work. Some of the biscuits are as small as 1/2-in. long and just a little over 1/16-in. thick. These might be perfect for your thin boxes.
Instead of planing off all that wood, I would suggest resawing it into two pieces and then planing just one side smooth. If your planer won’t go that thin, make a sled jig to mount the thin boards to it. This sled “carries” the wood through the planer. Typically this jig has a lip on one end to stop the thin board from kicking back out off the jig. It resembles a carver’s hook.
Chris Marshall: Another option to biscuit-joining those thin workpieces together is to just edge-glue them. It’s not particularly tricky to do for panels as small as yours need to be. Even if you’re starting with stock that’s only 1/4-in. thick, spread the glue along the edges in a thin coating, rub the boards back and forth to smear the glue further, and then put a small C-clamp or even a spring clamp over the joint at either end of the panel. Those clamps will help keep the edges aligned while you add a few longer clamps along the panel’s length to squeeze the seam together. Once that glue seam dries, it will be plenty strong for a little box without any additional mechanical reinforcement (biscuits, dowels, etc.).
Here’s another suggestion, even if it wastes a bit of wood: I’d resaw the boards down their center, as Tim suggests, so you can book-match the pieces and economize the material as much as you can. Plane the two 3/8-in.-thick pieces smooth (realistically, more like 5/16-in. when resawing a 3/4-in.-thick board with a typical band saw blade). Glue the panel together while the pieces are still thicker than they need to be, then run that through your planer to reduce the thickness further still (provided, of course, that it is narrower than your planer’s cutting width). Tim’s sled suggestion works great. Even a couple of strips of carpet tape, stuck to the sled at the ends of the panel, are enough to hold the panel securely when you feed the sled through the planer. When I need a sled, it’s just a piece of scrap MDF or melamine shelving with carpet tape applied to hold the workpiece in place. Super simple. I’ve done this many times, for both thin panels and when making long, thin sticks of wood for glass retainers, square plugs and the like.