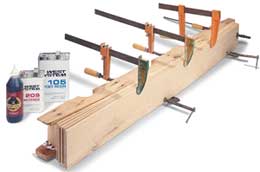
How can I bend 3/8-inch oak with a cutout design, which is for the back of a rocking chair, without steaming it? The cutout design makes it impossible to cold bend without breaking it.
Chris Mroz: Use red oak Compwood to cold bend the seat back. It will bend cold, by hand, in these thin dimensions. But you could go a lot thicker. Compwood that is 1-inch thick can bend to a 5-inch radius, so a seat back radius will not challenge the material. Support the inside of the bend with a bending form made on a band saw from scrap plywood or lumber. Clamp the plank to the form and let it dry to about 7 percent moisture content, or until it is equalized with its environment. You can put in the cutout design before or after bending, but it will be easier to create the cutout on the flat plank and then bend it, but either way, Compwood will machine just like any kiln-dried hardwood.
For more information on Compwood and what it does, check out the Industry Interview on Fluted Beams in this issue. – Editor
Andy Rae: It sounds like you have a strong case for laminations. Rip your stock into thin strips. Do a test-bend, but somewhere in the region of 3/16 in. thick is a starting point. Glue them back together in the order they were sawn. Use a rigid glue, such as plastic resin or two-part, slow-cure epoxy, and a shop-made bending form and plenty of clamps. A hard glue minimizes spring-in or spring-back, or the tendency for the lamination to move away from the desired curve after the glue has cured. It would be easiest to make your cutout design after laminating the strips, perhaps with a straight bit, a router and another homemade jig to guide the cut.