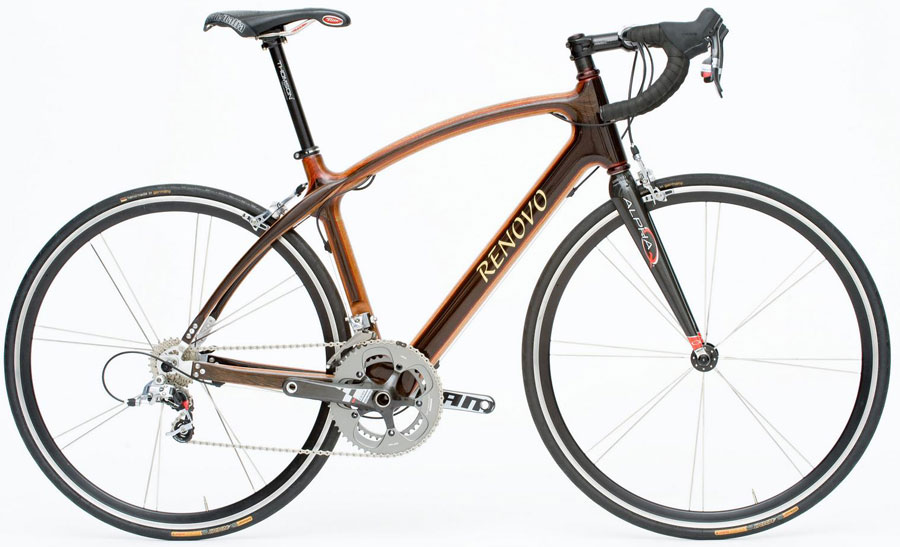
Woodworking and bicycle-building may seem like an unlikely pairing these days, but Ken Wheeler and his staff of four at Renovo Bicycles is doing just that. His Portland, Oregon-based business has been building wooden bike frames since 2008. While his is not the only company building wooden bikes, Renovo frames are catching the attention of hard-core cyclists around the world due to their durability, stiffness and light weight.
Ken started Renovo Bicycles after successful careers designing and manufacturing lighting fixtures and composite kit aircraft. After learning to use a CNC machine for building an airplane organization system, Ken set his sights on a new project: bicycle frames. “I looked around the shop and realized I probably had everything necessary to produce a sustainable bicycle of wood, and based on what I’d learned about wood, it would be an excellent ride, along with other advantages.”
Ken built Renovo’s first frame out of Baltic Birch plywood to test the CNC and the frame-building process. Baltic birch ply proved to be too flexible — not exactly a desired quality for bike frames. From there, Ken turned to jatoba wood to address stiffness issues. This second frame accomplished everything he was hoping for, and the company was off to the races. Renovo now offers frames made from many wood species such as sapele, bubinga, bloodwood, purpleheart, curly maple, wenge, hickory, bamboo and others. Ken won’t divulge which species he favors. “Our favorite bikes are the last ones we just built.”
Aside from minor joinery changes, the frame-building process has remained pretty consistent since the beginning. Each piece of wood is carefully selected to ensure its grain, color, moisture content and figure are suitable for a frame. Frames consist of two halves that are bonded together along the long axis of the bicycle. Four pieces of wood are connected with finger joints and epoxy, then cured in a custom-built kiln. Once the pieces are assembled, they begin a long journey through the laminating room, Routech CNC machine and oven, six times each. “Along the way they enjoy the attention of four different saws, a planer and a wide-belt sander,” Ken says.
From there, all of the detailing, sanding and finishing is done by hand. Taking a cue from boat- and aircraft-building, the final finish is two coats of epoxy followed by three coats of polyurethane. Ken says that the production process for building a wooden frame takes significantly more time than metal or carbon frames, especially those that involve additional wooden accent layers.
Recently, Renovo added all-wooden stays (the part of the frame that holds the rear wheel) to its frames. This was originally avoided to save on design and programming time, but they add design flexibility and improve frame stiffness. Wooden stays also contribute to the visual impact of the frame; now the grain runs the entire length of the finished bicycle.
Even though bike frames were originally made of wood, Ken says there are plenty of skeptics that are convinced anything other than carbon, aluminum, titanium or steel has no place in a modern bike frame. However, Renovo has performed a battery of stiffness tests that confirm that their wooden frames perform favorably against non-wooden frames.
As yet, Renovo bikes haven’t made an appearance in the Tour de France or other high-profile races. But, Ken says they have been called “race quality” by accomplished triathletes, and he expects to see them in races over the next year. If that turns out to be the case, Renovo’s unique bikes will surely be turning the heads of cyclist and spectator alike. Not to mention woodworkers, of course.