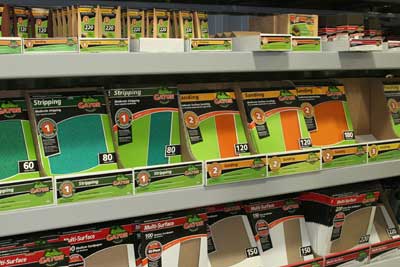
Almost a year ago now, I had the opportunity to tour Ali Industries, a sandpaper manufacturing plant on the outskirts of Dayton, Ohio, just a couple of hours from my home. Up until that time, I had never really given much thought to how sandpaper was made. Like most woodworkers, I certainly use plenty of it, but I had never really stopped “mid swipe” to process what might actually go into making this ubiquitous but essential woodworking material. Well, these days when I reach for a piece of sandpaper, it often brings to mind that field trip last spring.
Ali Industries has been making consumer sandpaper and sanding products for nearly 50 years. The company’s founder, Frank Ali, got into the business back in 1961 during NASA’s space race heyday. Frank saw a need for specialized abrasives in the aerospace industry, and he began to make abrasive cartridge rolls for deburring spacecraft and jets. Yep, rockets and fast airplanes—the stuff I loved to dream about as a kid. As Frank’s son Phillip, who is Ali Industry’s president and my tour guide, explained, if you don’t polish a rocket to near perfection, even the smallest burrs or irregularities can cause it to burn up when it enters or leaves the atmosphere. Clearly, not good a good outcome for an ambitious space program or astronauts hoping for safe return to terra firma.
Frank started the business conservatively … in his garage. But, call it good timing, a keen entrepreneurial spirit or both—the business took off and moved from garage to factory in just a short time. And, over the years that followed, his industrial abrasives helped to put astronauts on the moon and enabled military and experimental planes to slip more smoothly through the wild blue yonder. Frank even met fellow Ohioan, astronaut and former senator John Glenn back in the glory days. They remained friends for the rest of Frank’s life.
Once the Apollo Space Program proved that moon travel was both feasible and repeatable, funding began to dry up for moon missions. In the late 1960s, Frank responded by shifting the family business over into retail abrasives. His premium quality sanding products weren’t limited to industrial applications: woodworkers, auto buffs and other hobbyists could benefit from them, too. And, of course, the manufacturing processes and quality standards were already in place. Ali began to sell sandpaper to various hardware store chains, as well as auto supply stores. That tradition of quality consumer abrasives continues today. Now, all four of Frank’s sons are actively involved in the family business, manufacturing thousands of feet of American-made sandpaper every day.
I also learned that these Ali boys are a resourceful lot. Frank and his sons literally designed and built, the colossus of a machine that manufactures their Gator Finishing Products. They call it, ominously, “The Maker,” and it has to be at least a football field long. If you’ve ever seen a continuous-feed web printing press in operation, you’d get the gist of how “The Maker” churns out sandpaper. Giant rolls of substrate, which can be either paper or cloth, feed into one end of the machine. It applies resin and a layer of grit (technically called grains), bakes it one or more times depending on the product, and then rolls up the completed bulk sandpaper on the other end. An electrostatic charge draws the grains up onto the glue-wetted substrate like a magnet. Unlike a gravity-based process, which would lay down the grains more or less randomly, a static current ensures that the largest flat facets of the grains end up glued to the paper. That way, their pointed tips face out. It’s an important detail that improves the abrasive longevity and performance.
From there, the sandpaper receives pressure-sensitive adhesive and either backing paper or a layer of fabric for hook-and-loop use. Sometimes the rolls are fed through another machine that bends the sheet several times to improve its flexibility. Then the sandpaper is die-cut into sheets, discs or belts before it’s packed up and shipped out to hardware stores and home centers. I was able to see the entire manufacturing process walking the building from one end to the other.
Ali Industries also makes an innovative line of pliable, ergonomic ZIP Sander™ hand-sanding products, plus concrete and metal grinding wheels. The company even prints its own packaging and manufactures metal product display units — all under one roof in Fairborn, Ohio. But, keeping everything close to home just makes sense to the Alis. Phillip sums up the company’s mom-and-pop approach to quality this way: “My brothers and I grew up in this factory. Abrasives are all we know, and that’s why we’ll continue to be an innovative leader in consumer abrasives.”
The trip to Ali Industries gave me new respect for sandpaper—what admittedly has to be the least appreciated of woodworking supplies. Sure, the process of sanding might be tedious, but quality abrasives can make the job faster and easier. There’s definitely more technology and process that goes into sandpaper manufacturing than I ever would have imagined.