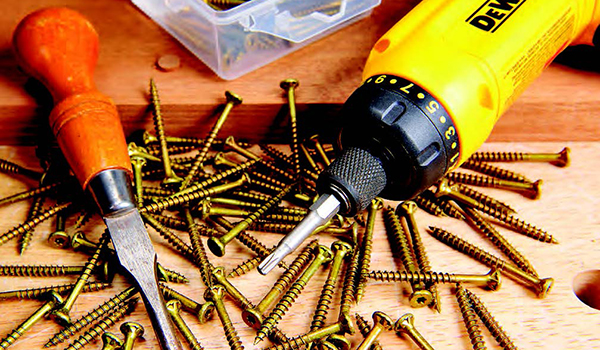
What kind of screws should you use on your next project?
It’s easy to be confused. Screws are undoubtedly the most versatile fasteners used in woodworking, but there are a lot of choices. Wood screws are handy for quickly building jigs and clamping forms, joining cabinet and furniture parts, mounting hardware and trim, and much more. Screws form strong connections between parts made from solid wood, plywood and other sheet goods without the need for cut joinery. From heads to drives, points to threads, platings to coatings, our author gives you a thorough education in the options available in the world of modern screws. or adhesives (and unlike glued joints, screws are removable, so you can take apart whatever you’ve built). Screws are also good for reinforcing parts assembled with traditional joinery — for example, pinning tenons in their mortises.
Choosing the right wood screw used to be simple pick a zinc or brass screw with the right size and length for the job at hand. But technological developments in construction and wood products manufacturing have spawned an extensive range of new screws in recent decades. There are so many choices, it’ll positively make your head spin!
I’ve written this article and shot this video to serve as a short primer on wood screws. Close examination of the various parts of a screw — the material it’s made from, the design of its head, drive style, point and threads, the platings and coatings that protect it from corrosion — will give you a better understanding of all the design and technology that goes into the manufacture
of every single screw. Hopefully, this exploration will better empower you the next time you need to choose the right screws for the project at hand.
Screw Types & Materials
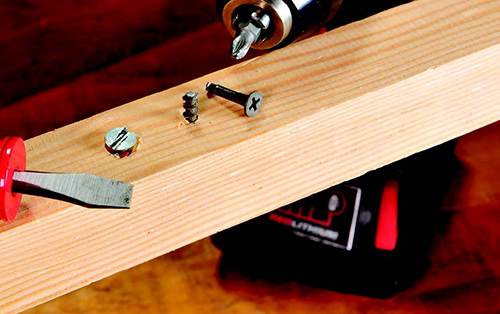
Among the many materials wood screws are made from — brass, bronze, aluminum, etc. — steel screws are the most useful for woodworking and interior DIY projects. They’re strong, affordable and readily available in a vast range of sizes. But old-fashioned tapered steel wood screws can be a pain to use. Many woodworkers switched to inexpensive drywall screws when they became readily available a few decades ago. Made from harder steel that can penetrate wallboard and studs, drywall screws drive in quickly and without the need for predrilled pilot holes. However, they’re relatively brittle and will snap when subjected to high drive forces or stress, making them a poor choice for projects requiring strong construction.
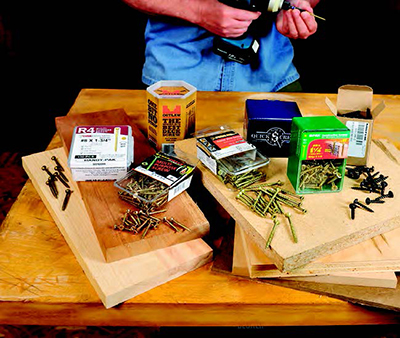
Fortunately, a different kind of screw has largely replaced traditional tapered and drywall screws. “Production screws” have points and threads sharp and strong enough to penetrate the hardest woods and manmade materials — even some metals. Their heads and shanks are durable enough to withstand high torque delivered during driving with a power drill or impact driver, and can withstand the punishing stresses that screw joined furniture or cabinet parts may be subjected to. Hardened-steel screws with brands including GRK Fasteners™, SPAX®, PowerPro™ and Saber Drive™ are often sold as “construction screws” or “multipurpose screws.”
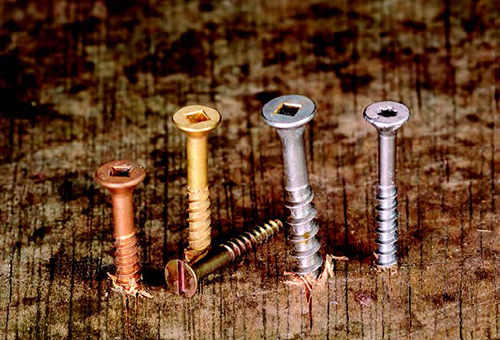
Unless they’re specifically plated/coated for exterior use, hardened steel screws aren’t especially weather resistant, and they are best reserved for indoor projects. Deck screws are basically production screws that have been plated and/or coated to increase their corrosion resistance. They’re great for outdoor projects, like playhouses or decks. For even greater resistance to rust and corrosion, the two best screw materials are silicon bronze and stainless steel. Weaker than regular steel screws, chromium alloy stainless steel screws come in two popular grades: Grade 305 stainless is good for applications where coated deck screws don’t have sufficient corrosion resistance, while grade 316 (sometimes referred to as marine-grade stainless) are best for projects that are exposed to salt air or in areas where severe corrosion is likely to occur.
Head Type
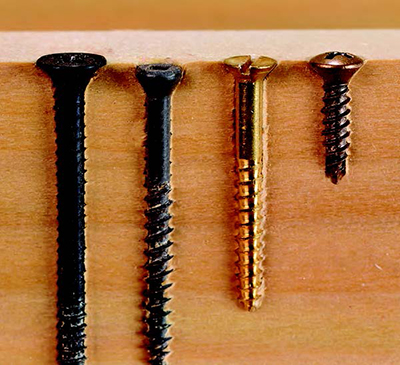
Regardless of a screw’s material, size or length, the shape of its head has a significant impact in how well it works in any particular application. Head designs can be divided into two groups: those that sink flush with the work surface and those that stand proud of it. In the first group, trim head screws and bugle head screws have heads designed to automatically sink flush in all but the hardest materials (e.g., rosewood, ebony). Bugle head screws drive in quickly and have good holding power in most materials. Trim head screws are a good choice when you only need modest holding power and don’t want the head of the fastener to show too prominently. When driven into pre-drilled holes, they are a better choice than finish nails for setting door jambs or mounting trim and moldings: trim head screws are less likely to split thin or delicate wood parts.
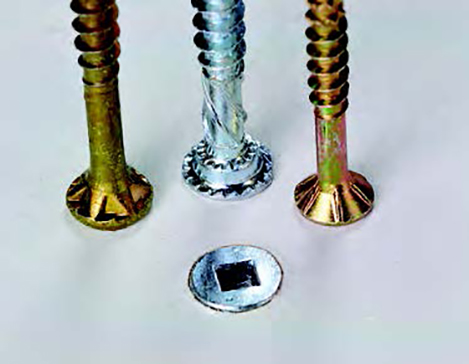
Traditional flat and oval head screws lend a nice clean look to projects but require a conical recess for their heads drilled with a countersink. In contrast, most flat head production screws are self-countersinking: they create their own recess that allows the head to sit flush. Quickscrews’ unique “Funnel Head” screws, designed for use with veneered plywoods and coated sheet materials like melamine, have double serrations, with very fine teeth that cut into delicate surfaces without tearing them up.
Among the screw head types that sit proud of the work surface are traditional round head, pan head and cheese head (aka fillister head) screws. Each has a relatively small head with a flat bottom that bears against the surface of the workpiece. This offers a reasonable amount of hold in hardwoods, but in softer species, the smaller heads tend to crush the wood at the surface. When the joined pieces are stressed, the screw’s effective hold is reduced. Screws with larger heads offer more contact area with the work surface and a greater resistance to penetration and pull-through.
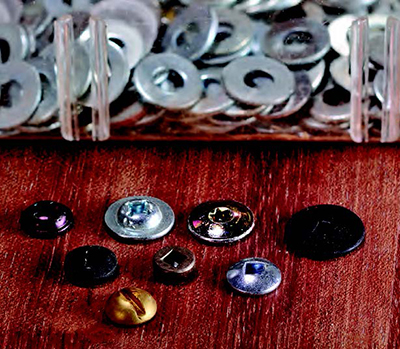
Truss head screws (aka “mushroom head” screws) have a head much like a metalworker’s pan head screw, only the overall head is flatter and larger in diameter. These are a great choice for mounting hardware such as drawer slides, where you want good contact with the hardware but need the screw head to not stick up too far. Washer head screws look like regular round head screws with small washers set under their heads. The added surface area on the underside of the head prevents them from sinking too deeply, especially when driven with power drivers.
Appropriately named “super washer head” screws have even larger diameter washer heads. They excel wherever two parts are joined but must remain adjustable, such as attaching a drawer front to a drawer box. Wafer head (and flanged head) screws have large, flat coin-like heads. Most wafer heads, including FastCap®’s “PowerHead” screws, are not only large, but are also very thin, giving them great retaining power and a low profile.
WATCH: VIDEO – WoodScrews 101
Drive Type
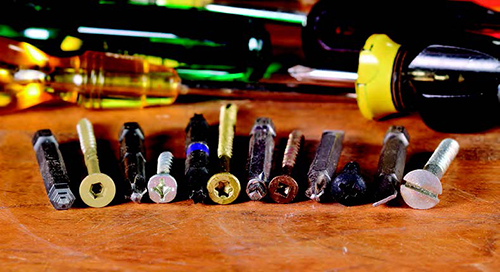
Unless they are building period-style furniture, few woodworkers still use traditional tapered wood screws with slotted heads, as they tend to slip off the screwdriver or driver bit and “cam out” easily, especially when driven with a cordless drill or impact driver.
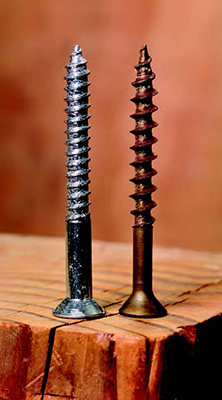
However, many woodworkers still do use Phillips head screws, which came into production in the 1930s and became popular because their cross-slot recess automatically centers on the tip of the screwdriver. They do have a tendency to cam out, especially when used with power drivers. But a little-known fact is that Henry Phillips designed his screws to do this on purpose! To help speed up automobile production, the cam out helped prevent workers from over-tightening Phillips head screws with early power drivers, which lacked torque-limiting adjustability. Today’s woodworkers reduce the tendency to cam out by carefully setting the clutches on their power drivers. POZIDRIV®, a modern variant of the Phillips drive, was developed to retain centering while reducing caming out. It is a good choice for larger/longer screws that require lots of torque when driven into hard materials.
Although there are dozens of modern drive styles found on screw fasteners (hex, polydrive, spanner head, etc.), two have become particularly popular in recent decades: Robertson square and TORX® star drives. The square “Robertson” drive was developed in Canada in the early 1900s, but Peter L. Roberston’s reluctance to license his screws to industrial users (like Henry Ford) kept it from becoming popular in the United States. Only in recent decades have companies like online fastener retailer McFeely’s started marketing them to woodworkers. TORX drive screws, with a distinctive six-point star pattern, came out in the late ’60s and quickly became a popular production fastener used on everything from cars to motorcycles to consumer electronics. The majority of TORX-drive woodworking fasteners are deck screws, but the drive style is gaining popularity for general-purpose construction and cabinet screws, too. Robertson drivers come in six sizes, but #1 (green), #2 (red) and #3 (black) drivers are used for wood screws from size #3 to size #14. TORX drivers come in two dozen different sizes (T1 to T100), but T15, T20 and T25 drivers cover most common wood screws.
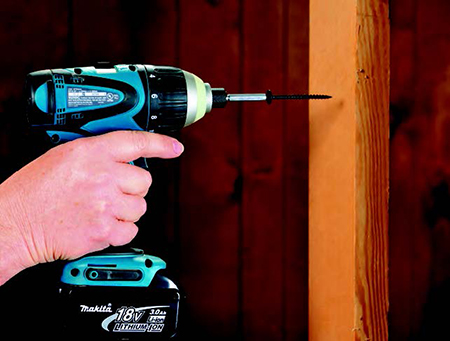
Both Robertson and TORX drives have two qualities that make them a great choice for woodworkers who use power drivers: stick fit and resistance to cam out. Stick fit is the ability of the driver bit and drive recess to form a temporary connection. Once you set a square or star drive screw on the tip of a drive bit, you can drive it without having to hold onto the screw. This not only frees up your extra hand, but it allows you to drive screws into all kinds of hard-to-reach places. TORX and Robertson drives both feature deep recesses into which the head of the driver fits snugly. The recess has near-vertical sidewalls, which means very little need for down pressure on the driver to keep it engaged. This not only significantly reduces the chance of cam out, but also reduces driver wear and damage.
Two other screw drive styles are worth mentioning: Pozisquare® and Outlaw drive. Pozisquare (aka combo drive) is a hybrid that combines a #2 Phillips and a #2 square drive in a single screw head recess. You can use either a Phillips or Robertson bit to drive them, but a special Pozisquare (combo) bit gives you better stick fit and cam out resistance. The new kid on the block, Outlaw Fasteners, raised more than $100k via Kickstarter and created their own line of unique deck screws. A three-tiered hexagonal head recess offers 18 points of contact for a super stick fit with virtually no cam out. In lieu of using their special driver, Outlaw screws can be driven with a regular hex driver.
Hiding or Covering up Screw Heads
Screws can provide a nice decorative detail on a project: imagine a row of shiny brass screws punctuating the edge of a walnut cabinet or a mahogany jewelry box. But when you don’t want screw heads to show, hiding them or covering them are both options. The simplest way to make flat head screws disappear is to set them into counterbored holes topped with flush-trimmed wood plugs that match the workpiece. You can drill pilot holes and counterbores in separate steps, or use a special bit that performs both tasks at once. Starborn Industries’ Pro Plug® system is a very nice kit designed to make the entire process quick and easy. It includes a special countersink/counterbore bit, a glue bottle tip designed for applying glue into the holes, screws and tapered wood plugs (available in a dozen different wood species).
If you’d rather enhance the presence of fasteners instead of entirely hiding them, decorative domed or button plugs or screw covers are the way to go. You can see a variety in the photo below. Decorative wood plugs glue into counterbored holes and can lend a nice detail while keeping screws hidden. Craftsman-style hole plugs (available from www.rockler.com) are sized to fit into 3/8″ holes, but they have square heads with pyramid-shaped tops that resemble the chiseled ends of small through tenons traditionally used in Mission style furniture. For modern style woodwork, try metal hole caps, available in various metallic finishes. I really like the look of black anodized aluminum plugs on a blond wood surface. Inexpensive and quick to install, FastCap plastic screw cap covers have small tabs that snap into the head recesses of square drive, flat head screws. White caps are perfect for camouflaging screws in melamine cabinets, and you can remove the caps if you need to disassemble the piece in the future.
Screw Points & Threads
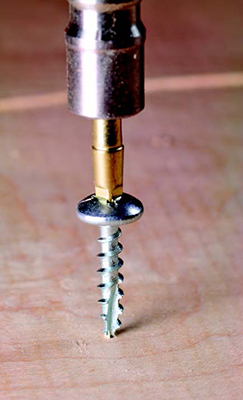
A wood screw’s point and threads have a mighty big task to accomplish. They must pierce the surface of wood, then pull the screw in, without causing the wood to split or splinter. Once driven, the threads have to hold the screw firmly in the wood so that it doesn’t pull out or allow the parts it joins to separate, even if they’re stressed. An old-school tapered wood screw needs a pilot hole when driven into all but the softest materials: their points are relatively dull and their shallow threads don’t offer much holding power.
In contrast, production, construction and deck screws have very sharp points and threads that are larger in diameter than the shank of the screw itself. This enables them to penetrate most materials without the need for a pilot hole, which adds up to a huge time savings when installing them! There’s no area of wood screw development that’s seen more innovation in recent years than thread and point design. Let’s look at both features in depth:
The Point
A good screw point bites into non-pilot-drilled surfaces rapidly, pulling the screw down quickly and creating an entry hole for the screw’s shank and threads. The majority of production/construction/deck screws rely on a Type 17 auger point to get this job done. This needle-sharp point penetrates even the hardest materials — and your fingers, so be careful when handling them! A self-tapping flute just behind the point cuts a hole through the surface while channeling debris up the shank of the screw. This helps to pull the screw in while reducing outward pressure that can cause splits and bulges. In lieu of a fluted auger point, some SPAX construction screws feature a 4CUT™ point with a squarish end that pushes aside wood fibers as the screw is driven instead of cleaving them.
The Threads
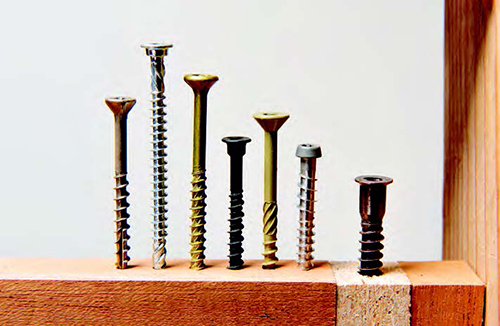
Once the point has pulled a wood screw down into the material, it’s up to the threads to continue driving it the rest of the way in. Conventional wisdom has always been that screws with fine threads are best for hardwoods — oak, cherry, maple, birch, etc. — while coarse-threaded screws drive and hold better in softwoods, plywood and composite sheet goods (particleboard, MDF, etc.). However, newer thread designs have changed the rules and made many production/construction screws suitable for use in a wide range of materials and applications.
Some threads, including the QuickCutter™, lead spiral and cross-cut threads, are designed to reduce the torque needed to drive the screw. In some specialized screw threads, a section of knurled shoulder thread, just above the regular thread of the screw, enlarges the hole slightly as the screw is driven, allowing the screw shank to turn more easily while helping to increase the clamping force between joined parts. Here are some of the newer thread designs and their intended advantages:
QuickCutter thread (Quickscrews production screws): Deep threads and an extra-long flute above the point.
Lead spiral thread (Quickscrews Funnel head screws): A spiral thread just above the tip pulls the screw into the wood quickly.
Cross-cut thread (Power Pro outdoor wood screws): A dual thread design with a standard outer thread and an inner thread that helps reduce friction at the root of the screw.
Hi-Lo thread (Rockler Hi-lo screws; Kreg® Hi-lo pocket-hole screws): A dualthread screw with a coarser, sharper outer thread and a finer inner thread. Creates a multipurpose screw that offers good holding power and less strip-out in all woods and sheet goods.
CEE™ thread (GRK R4™ and RSS™ screws; Outlaw deck screws): A knurled shoulder just above the regular thread of the screw.
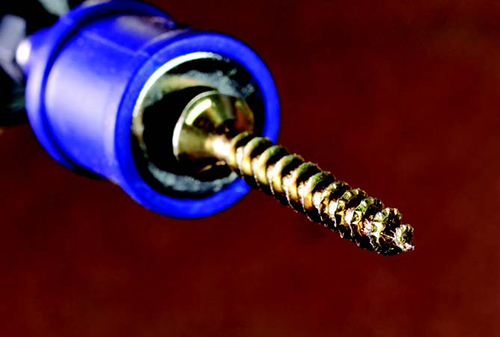
Reverse thread section (Starborn Cap-Tor xd deck screws): A section of reversed thread just under the head of the deck screw helps prevent dimpling and mushrooming (raised area around the screw head). A similar reverse thread on SPAX stainless steel wood deck screws helps prevent the screw from backing out as the lumber dries out.
Euro screw thread: Melamine, particleboard, and MDF are notorious for their poor holding power when joined with regular screws. In the 1970s, German hardware manufacturer Hafele introduced Confirmat oversized screws specifically for building ready-toassemble Euro-style furniture and cabinets. Confirmat (or similar Firmit) fasteners act like threaded steel dowels, forming a strong, stiff butt joint between parts.
W-Cut™ thread (GRK RSS and Cabinet screws) and Serrated thread (Saberdrive and SPAX screws): A saw-like serrated edge cut into the threads designed to slice through wood like a circular saw blade.
Plating and Coatings
In the final step of manufacturing, most steel wood screws receive some kind of plating (a metallurgical process done to bare metal screws) or coating (applied to either bare metal screws or already-plated screws). Screws are plated and/or coated for three reasons.
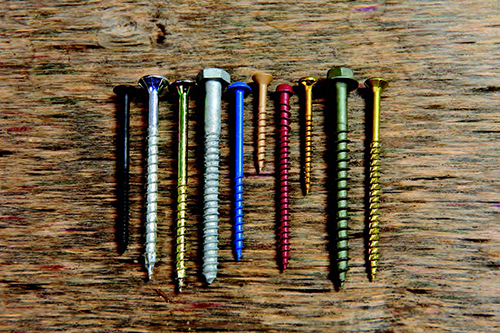
1. Prevent Corrosion
Regular steel screws rust quickly when exposed to moisture. Plating not only helps keep the screw itself from rusting, but prevents rust that forms on the screw from staining the wood around it. The most common plating on wood screws is bright zinc, largely a decorative finish that provides only a small amount of corrosion resistance. Zinc screws can develop a dull white corrosion (“white rust”) unless protected with a clear coating or a colored chromate, such as yellow zinc. Bright golden yellow zinc screws have more corrosion resistance than bright zinc, so this coating is common on construction screws. Black oxide (black phosphorous) plating prevents steel screws from rust staining wood, but offers little protection against serious corrosion.
Galvanizing processes, e.g., electroplating and hot dipping, have traditionally provided screws with the best protection against rust, but modern deck and construction screws are also available with high-tech coatings or plating/coating combinations for outdoor environments:
Blue-Kote™ (Kreg pocket-hole screws): Blue screws with three anti-corrosion layers; weather-resistant.
NoCoRode PLUS Pro-Master wood screws (sold by McFeely’s): almost 20 times more corrosion-resistant than standard yellow zinc plating; work well with most outdoor woods.
Epoxy Coated: Starborn’s Deckfast® Epoxy Coated screws provide corrosion resistance and come in four colors (gray, green, red and tan) to match treated lumber.
Climatek™: A GRK coating consisting of six layers of zinc and polymers; approved for use with highly corrosive pressure-treated lumber.
HCR™: SPAX “high corrosion resistance” screws have a dual barrier coating system with an electrically applied substrate and a proprietary organic topcoat designed to extend the longevity of the screw even when used with treated lumber.
Weather Maxx™ Bronze Ceramic Coat: Power Pro brand screws with multiple layers of zinc and polymer-based coatings. Recommended for use with ACQ, CA and CCA treated lumber, plus cedar and redwood where they won’t stain the wood.
2. Enhance Appearance
Other color choices are available besides silvery bright zinc. Brass-plated screws mimic solid brass screws but are stronger and cost less. Black oxide plated screws’ look works well with contemporary style projects.
To help hide fasteners without counterboring and plugging, some screws come with heads coated with epoxy paint. White or sand (tan) heads match the color of white or almond melamine sheet material. Starborn’s HEADCOTE® stainless-steel screws have heads colored to match commonly used decking lumber as well as PVC and composite materials.
3. Reduce Friction
The better the surface lubricity of a screw, the easier it is to drive and the less power it takes to drive it in. Slippery screws are also less likely to cam out, break or get stuck when they encounter knots or dense grain.
You can lubricate screws yourself by rubbing them with candle or beeswax before driving them, but it’s much easier to buy screws already treated with a lubricating coating. Berenson coats both their plain and zinc-plated screws with a thin wax coating, which reduces friction and leaves no residue. Square-X Drive screws and Highpoint screws have specially formulated dry coatings that make them easier to drive while preventing surface corrosion (they’re recommended for interior applications only). For outdoor projects, FastenMaster TrussLOK® construction screws have an anti-friction topcoat applied over their corrosion-resistant epoxy coating.