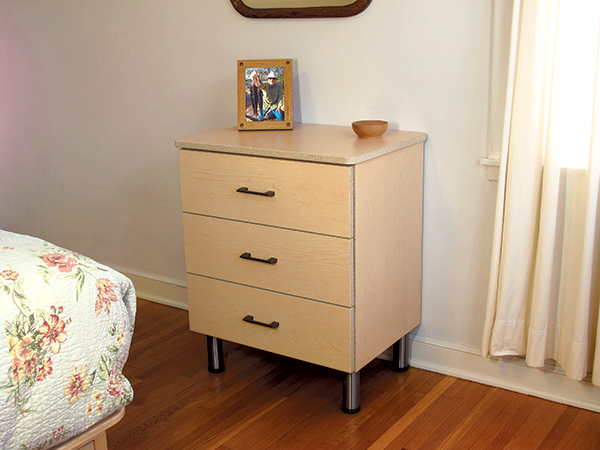
Sometimes building furniture is not about making a museum quality piece, but rather it’s about pure function and saving time and money. My wife and I needed a dresser to tide us over until I could build our “real” dresser, so off to the furniture store we went, only to find very expensive junk — basically made of cardboard — and nothing for less than $200. I’m thinking, no way am I putting money into anything like that when I can build one for half the price that will function 100 times better. Hence the piece you see here. It really fits the bill … and when I complete our official dresser, it will find a new life somewhere else in our home!
The construction is simple: just cut, rout, biscuit, drill, and assemble. I used 3/4″ melamine with a maple coating for the carcass, 1/2″ fiberboard for the drawers and 1/4″ melamine for the back and drawer bottoms — a half sheet of each. The panel stock I used was CARB 2 compliant (very low formaldehyde), so I didn’t need to apply any finish, and that’s a huge time saver.
Now, even though it costs just $100 for materials, in no way does that imply it’s an ugly beast. Sure, it’s not a Victorian bowfront dresser crafted from Honduras mahogany, but it does look pretty darn good considering what it’s made from, and I’m confident it will serve me well for many years. I was so happy with the results that I even made another one to be used as a sewing supplies cabinet, and I have future plans for shop cabinets based on the same design.
Construction Notes
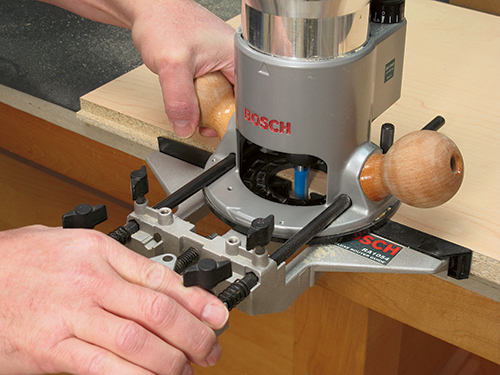
You’ll need the following tools to make this little dresser: a table saw, a router with an edge guide, a 1/8″-radius roundover bit and 1/2″-diameter straight bit, a pattern flush-trim bit, a router table, a biscuit jointer, drill press, brad nailer, staple gun, a jigsaw, and some bar clamps. Having a palm router to shape the 1/8″-radiused rounded over edges is also nice, but not absolutely necessary, and you could manage without using a router table if you chose instead to machine the drawer side end rabbets on your table saw, using a dado blade and a zero-clearance throat plate.
Although most of the pieces of this project are some form of rectangle cut on the table saw, it is always a good idea to take a moment to look at the Drawings and the Material Lists before you start cutting up material. Cutting the 1/2″ fiberboard and 1/4″ white melamine pieces from half sheets is easy since there’s room for waste with them, but getting all the 3/4″ maple melamine pieces from a half sheet is a bit tight. Use the three cutting diagrams provided here so you can minimize your waste. The secret, I found, was to start by putting the stretchers (pieces 4) next to the top (piece 1). Once I’d figured that out, the rest of the pieces fell into place.
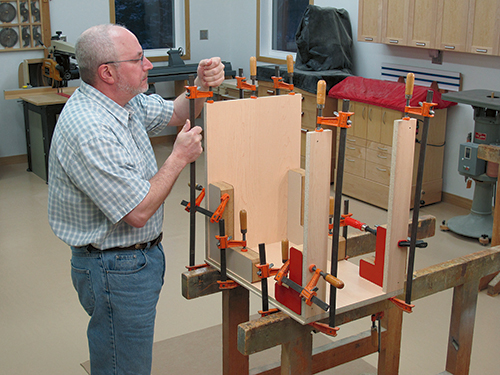
The dresser design is based around the use of 3/4 extension white, epoxy-coated, side-mounted drawer slides. They’re inexpensive, very easy to mount, and they operate really well.
The drawer components of the slides wrap around the bottom edges of the drawer sides. This allows the drawer bottom to be overlaid and nailed or stapled on, eliminating the need for cutting drawer bottom rabbets. If you use other slides, then note that the dimensions in the Drawings for the cabinet components of the drawer slides’ mounting heights are the same as the distances the drawer bottoms are relative to the carcass bottom (piece 2). Knowing that should help you figure out any alterations you may need to make if you use different drawer slides.
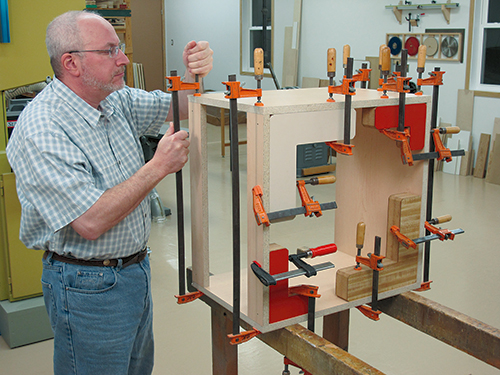
You’ll notice that the design is so simple that there is only one size drawer, and one size drawer face. This makes the work very easy. The only difference in the drawer construction is the alignment of the drawer faces to the drawers. The top two drawers are the same, with a drawer face bottom edge overhang of 1/4″, but the bottom drawer face overhang is 15/16″. Carefully follow the specified dimensions in the Drawings, and you should have no problem getting everything to align correctly when you assemble your dresser.
Assemble the Carcass and Drawers

Now that you have the overall picture of the project, it’s time to start making sawdust! Go ahead and cut all the pieces to size using the Material List on the previous and next page (pieces 1 through 5, and 7 through 10), and get started by routing the back rabbets (see photo 1). Machine the biscuit slots in the bottom (piece 2), sides (pieces 3) and stretchers (pieces 4). With that done, drill the screw holes in the stretchers. Glue, biscuit and clamp the carcass together as shown.
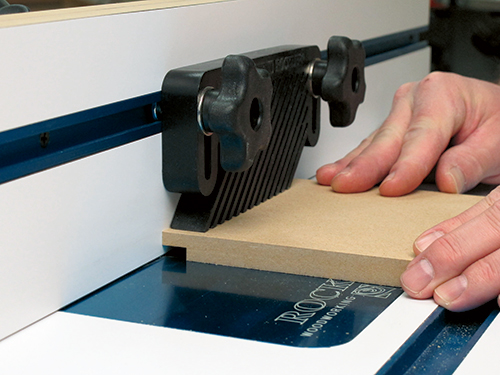
Drill the screw holes in the drawer fronts (pieces 8) (photo 4). The 5/16″-dia holes allow you to make minor drawer face alignment adjustments later.
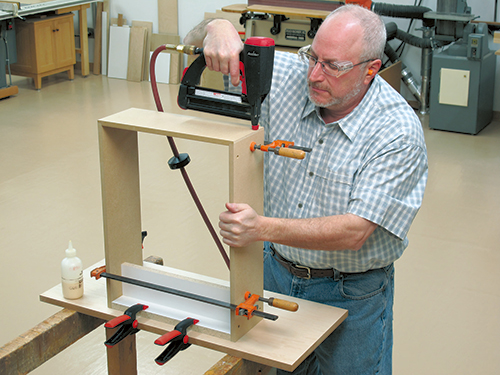
Rout the rabbets on the ends of the drawer sides (pieces 9) (photo 5). Now, assemble the drawers (photo 6), using 1″ brads to “pin” the drawer joints. Attach the drawer bottoms (pieces 10) to the drawers using 3/4″ staples.
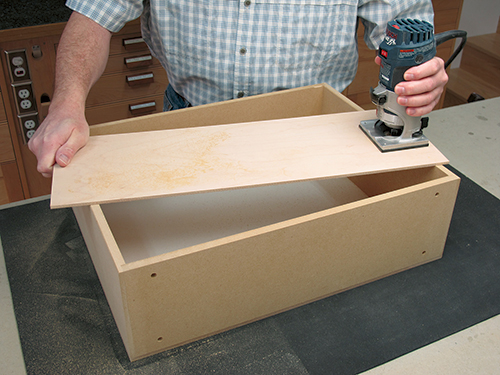
Rout 1/8″-radius edges around the top edges of the drawers (photo 7), but don’t rout the front edge of the drawer fronts. Then drill the pull bolt holes in the drawer faces (pieces 7) and follow up by routing the drawer face 1/8″ roundover on the corners and edges (photo 8).
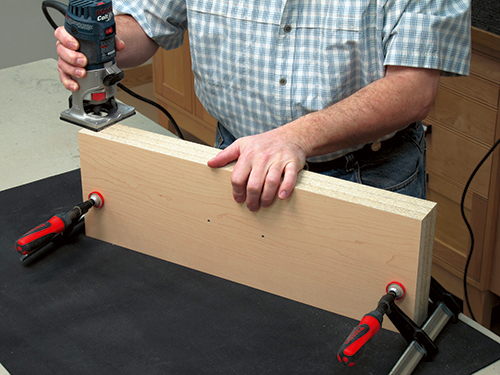
To mount the drawer faces, align and clamp them to the drawers and mark the pilot hole locations for the drawer-face mounting screws as shown in photo 9.
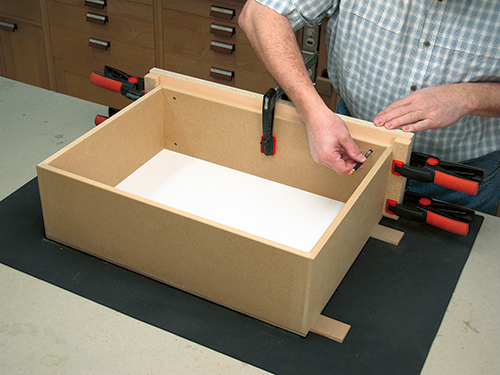
Note that on the two upper drawers the faces overhang the drawers by 1/4″ at the bottom, and the lower drawer’s face overhangs its drawer by 15/16″. Unclamp the drawer faces and use your drill press to drill the pilot holes, then attach the drawer faces. Mount the drawer slide cabinet components (pieces 12) to the carcass sides using spacers to locate them (photo 10).
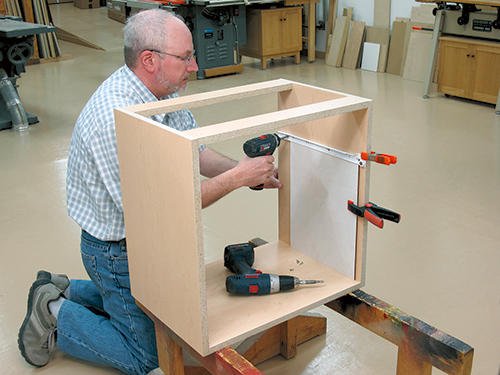
Only the long flat bottom edge of the slide should rest on the spacer when you mount the slides. Align the slide front ends flush with the carcass front edge. Now attach the drawer slide components to the drawer boxes. Align their front edges 1/16″ back from the drawer faces — it stops the drawers from banging against the face of the carcass. I used a 1/16″-thick spacer.
Final Assembly
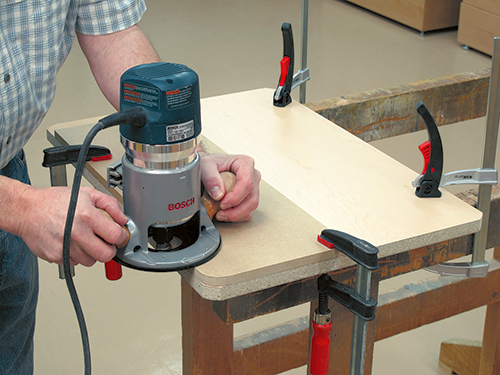
Staple the back (piece 5) to the carcass. Shape the top’s (piece 1) 1″-radiused corners as demonstrated in photo 11 and then cut the 1/8″ roundovers on the top’s edges. Then, screw the top to the stretchers. Note that the overhang is 3/8″ at the back.
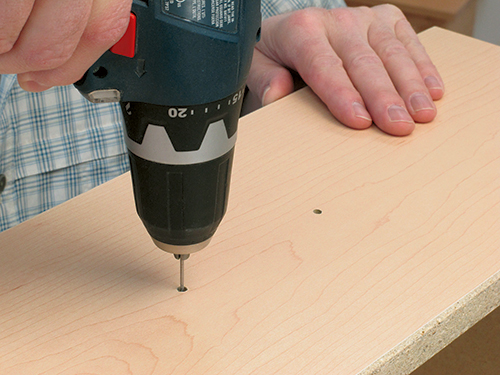
Drill the pulls’ bolt counterbore holes in the drawer fronts (photos 12 and 13). If you’re wondering why I drill the pull bolt counterbore holes this way, it’s because inevitably the pull mounting bolts loosen over time, and I want to be able to tighten them without having to remove the drawer face, and then having to realign the drawer face. When that is done, secure the pulls (pieces 11) to the drawer faces.
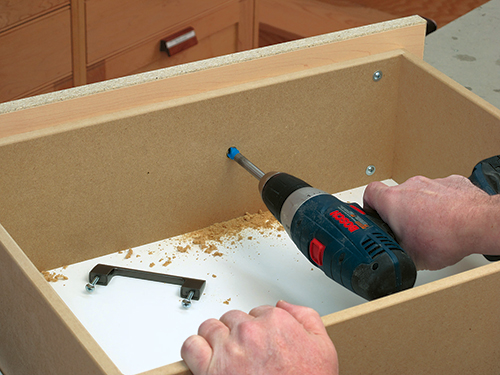
Mount the legs (pieces 6), being careful not to split the carcass sides when you’re driving the screws into the panel edges. This is an inherent problem with composite panels. Drill pilot holes for all the leg mounting screws, and make the pilot holes for the screws that go into the side panel edges 1/16″ less than the screw’s diameter. Apply wax, and drive the screws slowly. Insert the drawers and make any necessary alignment adjustments to the drawer faces. And … you’re done! (I told you this was going to be fast!)
Hard to Find Hardware